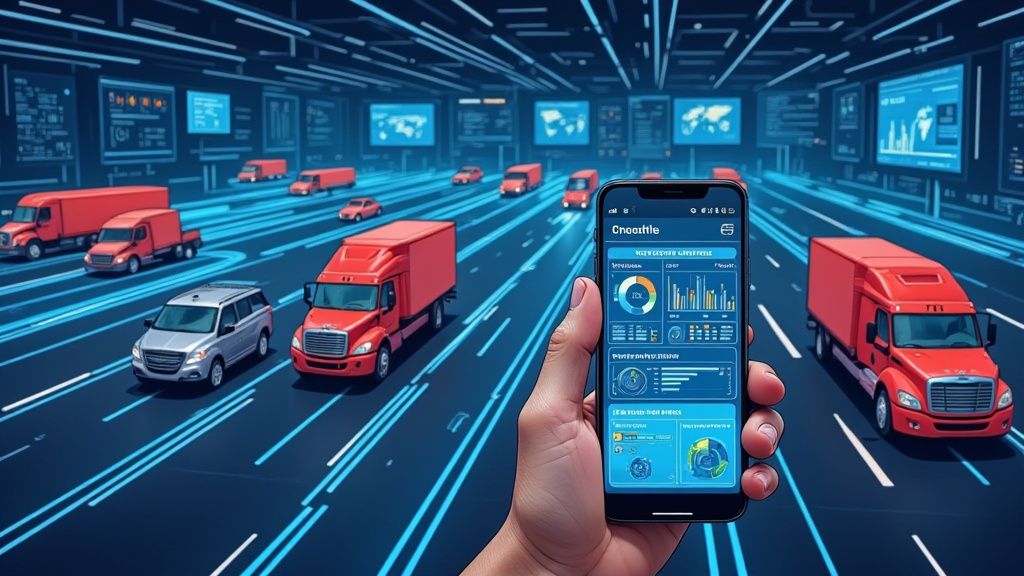
Vehicle Maintenance Tracking Apps: A Complete Guide to Modern Fleet Management
Smart Technology Revolutionizing Fleet Maintenance
Fleet maintenance has evolved significantly with the rise of vehicle maintenance tracking apps. These powerful tools combine artificial intelligence and machine learning to help fleet managers identify and address issues before they become major problems. Rather than simply reacting to breakdowns, businesses can now take a data-driven approach to keeping their vehicles running smoothly and efficiently.
Predictive Maintenance: From Reactive to Proactive
Vehicle maintenance tracking apps make it possible to spot potential problems early through data analysis. For instance, if a critical engine component is showing signs of wear, the app can alert managers before a complete failure occurs. This means repairs can be scheduled at convenient times, preventing unexpected breakdowns that disrupt operations and lead to costly emergency repairs. By monitoring vehicle health in real-time, fleet managers can maintain their vehicles more effectively while reducing maintenance costs.
The Role of AI and Machine Learning
Modern maintenance tracking apps use AI and machine learning to process information from multiple sources - vehicle diagnostics, driving patterns, and external conditions. For example, when the system detects a driver consistently braking hard, it can flag this as a potential brake system issue or driver training opportunity. This targeted analysis helps create customized maintenance plans based on how each vehicle is actually being used, moving beyond standard service intervals to truly optimize vehicle care.
Optimizing Driver Behavior For Enhanced Maintenance
The way vehicles are driven directly impacts their longevity and maintenance needs. Tracking apps monitor key driving metrics like speed, braking intensity, and idle time. This data helps fleet managers coach drivers on safer, more efficient driving habits that reduce vehicle wear and tear. They can also identify specific behaviors that need improvement and create focused training programs. By connecting driver performance with vehicle maintenance data, companies can better protect their fleet investments while improving safety.
Real-World Results: Cost Savings and Extended Vehicle Lifespan
Companies using vehicle maintenance tracking apps see clear financial benefits. Research shows that preventing major repairs through early detection leads to significant cost savings. Regular maintenance guided by data insights helps vehicles last longer and run more efficiently, using less fuel and requiring fewer repairs. For example, addressing a minor transmission issue early might cost a few hundred dollars, compared to thousands for a complete replacement after failure. This proactive approach, powered by maintenance tracking technology, helps fleet managers make smarter decisions that improve both vehicle reliability and their bottom line.
Making Telematics Work for Your Fleet
Managing a modern fleet requires more than just tracking vehicle locations. Telematics technology plays a key role by providing detailed insights into vehicle health and performance. When integrated with a vehicle maintenance tracking app, telematics helps fleet managers shift from reacting to problems to preventing them - saving valuable time and money in the process.
Real-Time Data Drives Better Decisions
The continuous stream of telematics data transforms basic vehicle diagnostics into clear maintenance guidance. For instance, if a truck’s engine temperature suddenly spikes, you’ll get an immediate alert so you can address the issue before it leads to a breakdown. Smart fleet managers use this information not just for maintenance planning but also to optimize routes and reduce fuel usage. By analyzing actual driving patterns and road conditions, maintenance tracking systems can identify more efficient routes that minimize vehicle wear while cutting fuel costs.
Getting More Value From Advanced Features
Many fleet operations aren’t taking full advantage of their telematics capabilities. While location tracking is important, features like remote diagnostics often go unused despite their ability to improve maintenance programs. These tools let mechanics evaluate vehicle issues remotely, often catching problems early before they become serious repairs. This prevents unnecessary shop visits and keeps vehicles on the road longer. Some maintenance tracking systems can even predict upcoming service needs by analyzing real-time performance data.
Connecting Driver Habits to Vehicle Health
Telematics data reveals important links between driving behavior and vehicle maintenance needs. Key metrics like speed, braking patterns, and idle time help managers identify areas where drivers can improve. This promotes both safer operations and better vehicle care. For example, frequent hard braking and rapid acceleration cause extra stress on brake systems and other parts. Using telematics data to coach drivers on smoother techniques extends component life and reduces repair costs. Taking this complete view - looking at both driver actions and vehicle diagnostics together - helps fleet managers get maximum value from their maintenance tracking systems while keeping their vehicles in top condition.
Building a Mobile-First Maintenance Strategy
Mobile devices have become essential tools for managing fleet operations effectively. Organizations increasingly recognize that mobile technology is a key factor in running efficient maintenance programs. A well-designed vehicle maintenance tracking app enables instant communication between drivers, mechanics, and managers while providing immediate access to critical vehicle data. This approach helps teams stay ahead of maintenance needs, minimize vehicle downtime, and achieve better financial results.
Why Go Mobile? Streamlining Communication and Access
When drivers can report issues in real-time, maintenance teams can respond much faster than with traditional paper systems. For example, if a driver notices unusual vibrations at highway speeds, they can immediately log detailed notes and photos through the app. This direct reporting means mechanics get accurate, timely information to diagnose problems quickly. The speed and accuracy of mobile reporting helps maintenance teams fix issues promptly before they become major repairs. Teams can also track maintenance history, schedule services, and access repair manuals right from their phones.
Choosing the Right Vehicle Maintenance Tracking App
Finding the best app for your fleet requires evaluating several key factors. First, check how well it works with your existing systems - can it connect to your telematics platform and accounting software? Good integration prevents duplicate data entry and helps information flow smoothly between systems. The app also needs to be simple to use, with clear navigation and readily available support. If drivers and mechanics find the app confusing or cumbersome, they won’t use it consistently. Take time to test different options and get feedback from the team members who will use it daily.
Overcoming Implementation Challenges
Moving to a new mobile system often faces some initial resistance, especially from staff used to paper processes. The key is showing teams exactly how the app makes their jobs easier - less paperwork, faster communication, and better organization of maintenance records. Providing thorough training and ongoing technical support helps build confidence in using the new tools. Another challenge is transferring existing maintenance records into the new system. Work closely with your app provider to plan a careful data migration that preserves important vehicle history while minimizing disruption to daily operations.
Real-World Success with Mobile Maintenance
Many fleets have seen significant improvements after adopting mobile maintenance apps like Auto Service Logger. These tools give drivers more responsibility for vehicle care, which leads to better reporting of potential issues. The direct communication between drivers, mechanics and managers means repairs happen faster with less confusion. One company found their vehicle downtime dropped 20% after implementing a maintenance app because problems were caught and fixed more quickly. The mobile access meant staff could update records, check vehicle status, and coordinate repairs from anywhere. This kind of flexibility and efficiency shows why mobile-first maintenance strategies deliver real value for modern fleets.
Mastering Predictive Maintenance Analytics
Managing a fleet effectively requires looking ahead, not just responding after problems occur. A vehicle maintenance tracking app makes this possible by collecting and analyzing data to identify potential issues before they become serious problems. This proactive approach helps fleet managers prevent breakdowns while reducing costs and keeping vehicles running smoothly.
Understanding the Data Behind Predictions
Modern vehicle maintenance apps pull information from multiple sources to monitor vehicle health. Engine diagnostic systems provide details about component performance, while telematics devices track real-world usage patterns like mileage, speed, and braking. When analyzed together, these data points reveal subtle changes that could signal developing problems. For instance, declining engine performance metrics might indicate the need for preventive service, even before obvious symptoms appear.
Interpreting Key Performance Indicators
Success with predictive maintenance depends on understanding what the data means in practice. Vehicle maintenance apps track key performance indicators (KPIs) that offer valuable early warnings. For example, if fuel efficiency starts gradually decreasing, it may point to fuel system problems that need attention. Similarly, data showing frequent hard braking could mean brake components are wearing faster than normal. By catching these patterns early, managers can address issues before they lead to breakdowns.
Balancing Preventive and Predictive Maintenance
While predictive analytics helps spot emerging problems, it works best alongside regular preventive maintenance. Think of preventive maintenance as routine health checkups, while predictive maintenance is like getting specific tests based on symptoms. A good maintenance app helps managers combine both approaches effectively. This means vehicles get exactly the service they need - not too much or too little. The result is less unnecessary downtime while still preventing major failures through timely interventions.
Implementing Data-Driven Maintenance Decisions
Making the most of predictive maintenance requires more than just having an app - it needs a systematic approach. Fleet managers should establish clear thresholds for key metrics, develop specific response protocols for different scenarios, and ensure staff know how to use the available tools effectively. While this takes some initial effort, the benefits make it worthwhile. Data-driven maintenance helps keep vehicles reliable while controlling costs. Most importantly, it gives fleet managers concrete information for making smart decisions about their operations.
Maximizing Your Maintenance Investment
Smart fleet management depends on making data-backed maintenance decisions that protect your vehicles and budget. A vehicle maintenance tracking app gives you the information needed to move from reacting to problems to preventing them - which saves money and helps your vehicles last longer.
Understanding the True Cost of Downtime
When vehicles unexpectedly break down, the costs add up fast. Lost work time, delayed deliveries, and emergency repair bills directly impact your bottom line. Think of a delivery truck that suddenly stops working - it disrupts schedules, disappoints customers, and causes financial setbacks throughout your operation. A vehicle maintenance tracking app helps avoid these problems by scheduling preventive care and spotting potential issues early, before they cause breakdowns that sideline your vehicles.
Using Data to Optimize Your Budget
The detailed records from a vehicle maintenance tracking app reveal important patterns in how your vehicles perform and what they cost to maintain. By analyzing this information, you can spot trends, plan for future repairs, and put your maintenance dollars where they’ll have the most impact. The app also tracks fuel use and driving habits to find more ways to cut costs. Rather than facing surprise repair bills, you can turn maintenance spending into a planned investment that reduces expenses over time.
Getting Better Vendor Rates Through Documentation
Complete maintenance records give you an edge when working with repair shops and parts suppliers. A vehicle maintenance tracking app creates detailed documentation showing how well you care for your fleet. When vendors see proof of consistent, preventive maintenance, they’re more likely to offer better pricing. This careful record-keeping often leads to meaningful discounts that increase the value of your maintenance program.
Building Resale Value Through Regular Care
Buyers pay more for vehicles with thorough maintenance records. A vehicle maintenance tracking app creates an organized history of all services and repairs, which builds trust with potential buyers. For example, a truck with digital records showing regular oil changes and tire rotations will sell for more than one with spotty maintenance documentation. This detailed care history helps you recover more money when it’s time to sell or trade in vehicles.
Showing Clear Returns on Your Investment
One of the most valuable features of a vehicle maintenance tracking app is its ability to measure results in actual numbers. By comparing what you spend on preventive maintenance versus emergency repairs, you can clearly show how proactive care saves money. For example, you might demonstrate how scheduled maintenance led to 40% fewer roadside breakdowns in the past year. This kind of concrete evidence helps justify the investment in maintenance tracking tools and shows their real benefit to your operation.
Implementation Roadmap and Success Metrics
Implementing a vehicle maintenance tracking app requires more than just downloading software. A thoughtful, phased approach with clear goals and measurement will set your fleet up for success. Here’s a practical guide for rolling out a maintenance tracking system effectively.
Phase 1: Assessment and Selection
Start by understanding your fleet’s specific challenges - are you dealing with frequent breakdowns, maintenance scheduling issues, or poor communication between drivers and mechanics? Document these pain points to guide your app selection. For example, if driver-mechanic communication is a major issue, look for apps with robust mobile features and instant reporting capabilities.
Take stock of your current technology ecosystem as well. If you already use fleet management or telematics systems, choose an app that works seamlessly with them to avoid creating data silos. Test different options with your team and gather their input - their daily hands-on experience will help identify the best fit for your operation.
Phase 2: Implementation and Training
With an app selected, create a detailed rollout plan covering data migration, user setup, and training. Work closely with your vendor to transfer existing maintenance records smoothly while minimizing disruption. Set up user accounts with appropriate access levels to maintain data security. Most importantly, invest time in comprehensive training.
Your team needs hands-on practice with the app’s core features to use it effectively. Provide clear documentation, guided training sessions, and ongoing support. Remember that the app’s value depends entirely on consistent, accurate data entry. Make sure drivers and mechanics understand how to properly log information and why it matters.
Phase 3: Monitoring and Optimization
Once the app is live, track key metrics to measure its impact. Monitor unscheduled downtime, preventive maintenance completion rates, and repair turnaround times. This data reveals whether the app is actually improving fleet operations. For instance, if breakdowns aren’t decreasing, you may need to adjust how issues are reported or maintenance is scheduled.
Regular usage analysis is also essential. Check if all team members are consistently using the app and identify any underutilized features. This insight helps target additional training or workflow adjustments. Ongoing monitoring ensures your maintenance tracking app continues delivering real value.
Success Metrics for Vehicle Maintenance Tracking Apps
Track these key metrics to evaluate your maintenance tracking app’s effectiveness:
Metric | Target |
---|---|
Unscheduled Downtime | Reduction of X% compared to previous periods |
Preventive Maintenance Compliance | Increase to X% |
Mean Time to Repair (MTTR) | Decrease of X% |
Maintenance Costs | Reduction of X% compared to previous periods |
Driver App Usage Rate | Increase to X% |
Following this structured approach and monitoring these metrics will help you successfully implement and optimize your vehicle maintenance tracking system.
Ready to improve your fleet maintenance management? Check out Auto Service Logger - a straightforward platform that centralizes your maintenance records and helps keep your vehicles running reliably.