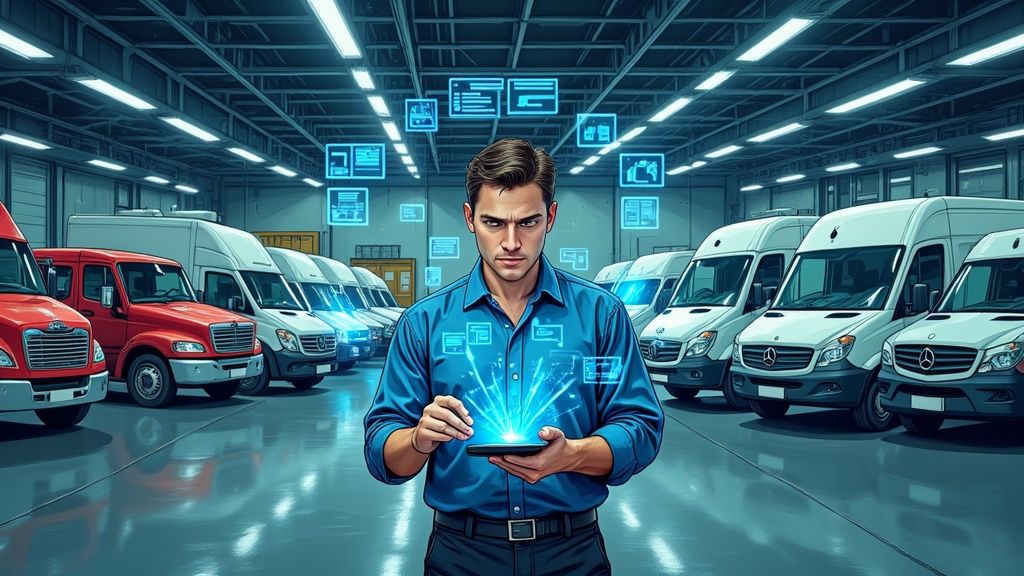
The Complete Guide to Fleet Maintenance Tracking: From Basics to Advanced Strategies
Understanding Modern Fleet Maintenance Tracking
Gone are the days of managing fleet maintenance with basic spreadsheets and paper logs. Fleet managers now use specialized maintenance tracking software to monitor their vehicles systematically and make data-driven decisions. This helps companies shift from fixing breakdowns after they happen to preventing issues before they occur. But what does effective fleet maintenance tracking actually look like in practice?
The Power of Proactive Maintenance
Consider a delivery company that depends on reliable vehicles to meet customer deadlines. Without proper maintenance tracking, an unexpected breakdown can derail schedules and damage client relationships. By implementing maintenance tracking software, the company can schedule regular service based on actual vehicle usage and catch potential problems early. This reduces surprise repairs and ensures vehicles spend less time in the shop getting fixed.
Using Historical Data to Make Better Decisions
A good maintenance tracking system creates a detailed service history for each vehicle. This data reveals important patterns and trends over time. For example, if several trucks develop the same issue after reaching 50,000 miles, fleet managers can proactively service all similar vehicles before problems emerge. Understanding these patterns also makes maintenance costs more predictable for better budgeting.
Key Metrics to Track With a Fleet Maintenance Tracker
The right maintenance tracking system gives fleet managers access to critical performance data. Monitoring these key metrics helps optimize operations and understand true ownership costs:
-
Total Cost of Ownership (TCO): This measures all expenses related to each vehicle, including fuel, maintenance, repairs, and value depreciation. Having accurate TCO data helps managers decide when to replace vehicles and whether to lease or buy.
-
Maintenance Costs Per Mile: Breaking down maintenance spending by mileage reveals issues with specific vehicles or maintenance practices. Sharp cost increases often signal underlying problems that need attention.
-
Preventive Maintenance Compliance: This shows whether scheduled maintenance happens on time. Following maintenance schedules helps vehicles last longer with fewer breakdowns.
From Reactive to Proactive: A Real-World Example
A delivery company recently switched from paper records to digital maintenance tracking. Before the change, they only fixed vehicles after problems occurred, leading to frequent unexpected repairs and delays. After implementing tracking software, they began scheduling maintenance based on actual mileage and usage data. As a result, breakdowns decreased significantly and delivery reliability improved. The detailed performance data also helped them make smarter decisions about when to replace aging vehicles. This shows how proper maintenance tracking helps companies not just maintain their fleets, but truly optimize their operations.
Building Your Preventive Maintenance Strategy
Creating an effective preventive maintenance plan requires more than just following the manufacturer’s recommended service schedule. Each fleet operates under unique conditions that affect how vehicles wear over time. Understanding these specific factors - from vehicle age and usage patterns to environmental conditions - is essential for developing a maintenance approach that extends vehicle life and reduces unexpected downtime.
Balancing Manufacturer Recommendations With Real-World Conditions
While manufacturer guidelines provide important baseline recommendations, they don’t account for the day-to-day realities of your specific operation. Consider a delivery truck making frequent stops in harsh winter weather - it experiences much more stress than one cruising highways in mild conditions. Simply following standard maintenance intervals could lead to problems in demanding situations or unnecessary service in gentler environments. This is where a fleet maintenance tracker becomes valuable, allowing you to document actual operating conditions and adjust service timing accordingly.
Frameworks for Creating Effective Maintenance Schedules
Building a solid maintenance schedule starts with the manufacturer’s suggested intervals as a foundation. From there, analyze the real vehicle data captured in your fleet maintenance tracker to spot important patterns. For example, if you notice certain parts consistently failing around the same mileage point in your operating environment, you can schedule replacements before problems occur. Keep in mind that older vehicles typically need more frequent attention, so factor age into your maintenance planning.
Reducing Downtime Without Compromising Quality
Smart scheduling through a fleet maintenance tracker helps minimize vehicle downtime while maintaining high service standards. One effective approach is combining related maintenance tasks into single service appointments to reduce the number of times vehicles are out of commission. Planning maintenance during off-hours or weekends also helps limit operational disruptions. The fleet maintenance tracker’s data enables you to order parts ahead of time and allocate resources efficiently. With tools like Auto Service Logger, you can take a proactive approach to maintenance scheduling that prevents unexpected breakdowns. This strategic planning saves money on emergency repairs while keeping your fleet running smoothly.
Using Technology for Better Fleet Management
Smart maintenance planning requires the right tools to be effective. Modern fleet operations rely on maintenance tracker software working together with telematics systems to deliver real results. This combination allows managers to integrate live vehicle data with maintenance schedules, enabling repairs to be done before problems occur. The result? Less downtime and longer-lasting vehicles.
Essential Features to Look for in Fleet Maintenance Software
When selecting fleet maintenance software, certain key capabilities make a real difference in daily operations:
- Automated Service Reminders: Let the software track maintenance schedules based on mileage, engine hours, or calendar dates. This frees up staff time while ensuring no service is missed.
- Complete Vehicle Records: Keep all important vehicle information in one place - from maintenance history to warranty details and documents. This makes it simple to access critical data when needed.
- Live Diagnostic Updates: Connect with telematics to get instant alerts about potential issues. This helps catch small problems before they become expensive repairs.
- Parts Management: Track inventory levels to make sure you have necessary parts on hand for scheduled work. No more delays waiting for parts to arrive.
- Data Analysis Tools: Use built-in reporting to understand maintenance costs, track vehicle performance, and spot trends. This helps make smarter decisions based on real data.
Making Your Software Work with Other Systems
For best results, your maintenance software should connect smoothly with other business tools. For example, linking fuel card data to maintenance records can show how service timing affects fuel efficiency. Adding accounting software integration gives you accurate cost tracking and helps calculate the true cost of operating each vehicle.
Getting Your Team on Board
Success with new maintenance software depends on having your team’s support. Start by showing them exactly how it will make their jobs easier and more efficient. Provide thorough training so everyone knows how to use the system properly. Ask for feedback regularly and address any concerns quickly. Make sure to explain the security features that protect sensitive data. When teams understand how the software helps them work better with less paperwork, they’re more likely to embrace it fully. A product like Auto Service Logger offers the essential features needed to track and analyze fleet maintenance effectively. With proper implementation, you’ll see real improvements in fleet performance and maintenance costs.
Mastering Data-Driven Decision Making
A good fleet maintenance tracking system does more than just store records - it provides concrete data that helps you make smart decisions to improve your operations and reduce costs. By tracking and analyzing key performance metrics, you can spot problems early, optimize maintenance schedules, and make informed choices about your fleet.
Calculating and Improving Total Cost of Ownership (TCO)
When managing fleet vehicles, it’s essential to understand the full cost of owning and operating each one. Total Cost of Ownership includes purchase price, fuel, maintenance, insurance, and even administrative overhead. A maintenance tracking system brings all these costs together in one place for easy analysis. For example, you might have two identical delivery vans, but notice that one consistently uses more fuel. By connecting maintenance records with fuel data, you can identify if there’s an underlying mechanical issue causing the higher fuel consumption. This insight helps you fix problems early and make smart decisions about when to replace vehicles versus continuing repairs.
Tracking Maintenance Costs Per Mile
Looking at maintenance costs per mile lets you compare vehicles directly and find ones that are costing more than they should. Let’s say you notice that one truck’s maintenance costs are 30% higher per mile than similar vehicles. The tracking system helps you dig deeper - maybe the driver needs additional training, or perhaps there’s a recurring mechanical issue that needs attention. Finding these issues early prevents small problems from becoming expensive repairs. Regular tracking of per-mile costs acts like an early warning system for your fleet’s health.
Identifying Trends and Predicting Potential Issues
A fleet maintenance tracking system helps you spot patterns over time to prevent problems before they happen. Consider a delivery company working in an area with harsh winters. Their tracking data shows that certain vehicles need brake repairs more often during winter months. Armed with this information, they can schedule preventive maintenance before winter hits and stock up on brake parts they know they’ll need. Systems like Auto Service Logger make it easy to gather this data and generate reports that reveal important patterns. This shifts fleet management from reacting to problems to preventing them proactively, saving money and keeping vehicles running smoothly. The data helps you allocate resources effectively and maintain a reliable fleet that meets your business needs.
Creating a Culture of Maintenance Excellence
A robust fleet maintenance tracking system requires more than just new software and processes. Success depends on building a company culture where everyone understands and values proper maintenance practices. When teams internalize the importance of accurate record-keeping and proactive upkeep, they create lasting positive change.
Fostering Team Buy-In and Accountability
Getting staff on board with a new fleet maintenance system can be challenging at first. Some team members may hesitate to adopt unfamiliar tools and workflows. The key is helping them see concrete benefits - like how the system makes their daily work easier by reducing manual paperwork and providing quick access to important vehicle information. Show real examples of how the software streamlines common tasks they perform.
Setting clear expectations around data entry and maintenance responsibilities is also essential. When each person knows their role and regularly receives constructive feedback on data quality, it creates accountability. Much like a well-maintained engine needs all parts working together, the maintenance system thrives when the whole team collaborates effectively.
Training for Success
Thorough training empowers teams to maximize their use of fleet maintenance tracking tools. Beyond teaching the technical aspects of the software, training should cover fundamental concepts of preventive maintenance and how to analyze maintenance data meaningfully. This deeper understanding helps staff recognize the value of the information they collect.
The most effective training programs use varied approaches - from hands-on practice sessions to video tutorials to one-on-one coaching. Meeting different learning styles and providing ongoing support ensures staff can confidently use the system. This investment in training directly impacts maintenance outcomes by promoting accurate data entry, which enables better maintenance planning and extended vehicle life.
Communication and Continuous Improvement
Regular, open communication keeps maintenance excellence on track. Create dedicated channels for staff to share feedback about challenges they encounter and suggest system improvements. For example, set up a team chat group or regular check-in meetings focused on maintenance tracking. This involvement gives staff ownership in the process.
Remember to recognize team members who consistently maintain high data quality standards and follow maintenance best practices. Track and share key metrics like maintenance cost per mile and preventive maintenance completion rates to show the real impact of everyone’s efforts. Just as regular vehicle maintenance prevents breakdowns, steady communication and feedback help teams operate at their best.
Implementation Roadmap and Best Practices
A successful fleet maintenance tracking system requires thoughtful planning and methodical execution. The key is integrating the system effectively into your existing operations while building a data-driven maintenance culture. Here’s a practical roadmap and key practices for implementing fleet maintenance tracking.
Phase 1: Assessment and Planning
Start by evaluating your current maintenance processes in detail. Document your existing workflows, identify specific challenges, and outline clear goals. For instance, if excessive downtime from reactive maintenance is an issue, or if you struggle to track maintenance costs accurately, note these as priorities.
Next, develop a structured implementation plan with clear milestones and timelines. Create an implementation team with staff from maintenance, operations, and management to ensure broad support. This collaborative approach builds momentum and helps catch potential issues early.
Phase 2: Software Selection and Setup
Choose software that matches your needs and budget. Focus on essential features like automated maintenance reminders, detailed vehicle history tracking, and clear reporting tools. Check that the system works with your current tools, particularly any telematics or accounting software you use.
During setup, take time to properly configure the system and transfer existing maintenance records. Provide thorough training so your team understands key functions like entering data, running reports, and managing maintenance schedules. Clear documentation and hands-on practice sessions help ensure everyone can use the system effectively.
Phase 3: Deployment and Optimization
Once live, monitor how the system performs in daily use. Gather regular feedback from maintenance staff, drivers, and managers about what’s working well and what needs improvement. For example, you might find certain reports need adjusting or data entry steps could be simplified. Make these refinements based on real usage patterns.
Set specific metrics to track success, such as preventive maintenance completion rates, maintenance cost per mile, and vehicle availability. Regular review of these numbers helps show the system’s impact and highlights areas needing attention.
Phase 4: Ongoing Monitoring and Refinement
Maintaining an effective fleet maintenance tracking system requires continuous attention. Review performance metrics regularly, collect user feedback, and stay current with software updates. This active management helps you get full value from the system and adapt it as your needs change. As your fleet grows, ensure the system can handle increased vehicles and maintenance activities while maintaining performance.
Ready to improve your fleet maintenance tracking? Auto Service Logger offers comprehensive maintenance tracking, vehicle record management, and data analysis tools. Visit us today to learn more about optimizing your fleet maintenance program.