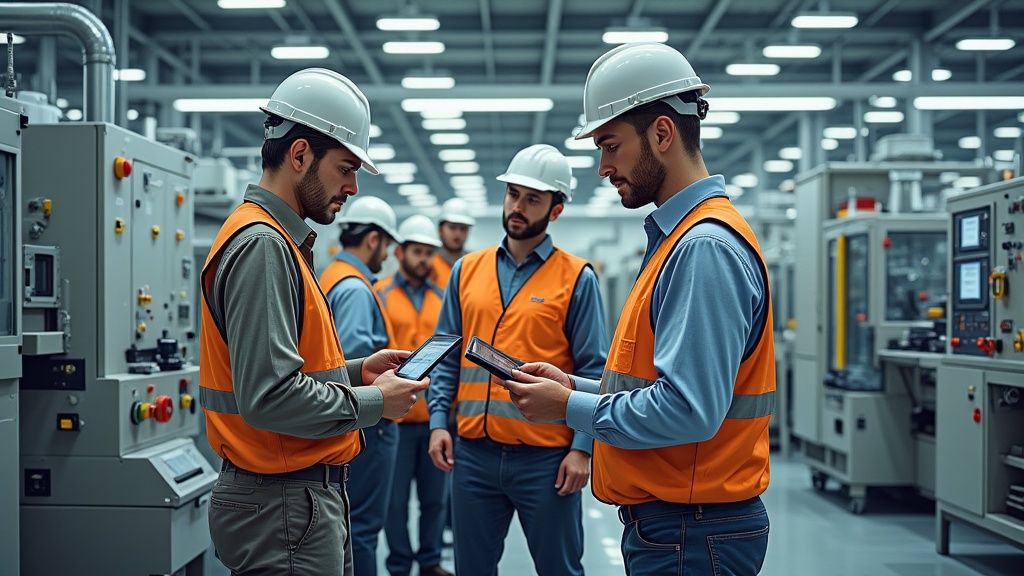
Preventive Maintenance Best Practices: Your Proven Implementation Guide
Understanding The True Value of Preventive Maintenance
Making the switch from reactive to preventive maintenance can dramatically improve how businesses maintain their equipment and assets. Rather than constantly responding to breakdowns, organizations can plan ahead and fix potential issues before they cause problems. This approach is similar to regular medical checkups - addressing small issues before they become serious complications.
The numbers tell a compelling story about preventive maintenance. 76% of manufacturing companies worldwide now prioritize preventive maintenance in their operations. Even more impressive, this approach typically reduces maintenance costs by 12-18% and provides up to a 5x return on investment. For more detailed data, check out these maintenance industry statistics.
The Impact on Operational Efficiency
Good preventive maintenance has clear benefits for business operations. When equipment runs reliably with minimal unexpected downtime, companies can stick to production schedules and meet customer needs consistently. Well-maintained machines also use less energy, which helps reduce operating expenses and improve profit margins.
Data-Driven Decisions and Practical Experience
The most effective preventive maintenance programs combine data analysis with hands-on expertise. By studying maintenance records and repair histories, teams can spot patterns that help them schedule upkeep at the right times. For instance, if data shows a specific part typically fails after a certain number of hours, maintenance can be scheduled just before that point. This smart blend of analytics and real-world knowledge helps teams work more effectively.
Shifting From Reactive to Proactive
Changing from reactive to preventive maintenance requires a different mindset across the organization. Teams need to embrace planning ahead and investing in prevention, even when reactive repairs seem more pressing. While this change takes time and effort, the long-term advantages - like lower costs, better efficiency, and longer-lasting equipment - make it worthwhile. This approach also helps maintenance teams take charge of their work rather than just responding to emergencies, which builds confidence and job satisfaction.
Building The Foundation: Essential Program Components
Creating a reliable preventive maintenance (PM) program requires more than just scheduling and following through. Success depends on having key elements that work together effectively - much like constructing a building needs proper planning, materials, skilled workers, and regular inspections to ensure it remains stable over time.
Structuring Your Maintenance Hierarchy and Documentation
A clear maintenance hierarchy is essential for any organization. This framework defines who does what and who to contact for help - much like having detailed construction plans. Equally important is having thorough documentation that includes step-by-step procedures, equipment details, and historical records. These documents serve as your program’s instruction manual, providing critical information when needed. Read more about setting up an effective site structure.
Training Programs and Resource Allocation
Quality training ensures your maintenance team has the skills to do their jobs correctly. Having well-trained staff is similar to having skilled builders who can turn plans into reality. Resource allocation is another vital element - this means carefully planning how to use your budget, people, and tools. Just as construction projects need materials within budget constraints, PM programs require proper resources to function effectively.
Balancing Planned Maintenance and Operational Demands
The most effective PM programs find ways to balance scheduled maintenance with daily operations. This requires minimizing disruptions while keeping equipment running smoothly - similar to renovating a building that’s still in use. By planning ahead to address potential conflicts, organizations can avoid unexpected downtime and maintain steady operations. This approach helps create a better work environment for maintenance teams since they spend less time dealing with emergencies, which leads to improved job satisfaction and better staff retention.
Measuring Success: Beyond Basic ROI Metrics
Tracking Return on Investment (ROI) helps show the financial benefits of preventive maintenance, but it’s only part of the story. To get a complete picture, maintenance teams need to look at multiple factors that affect business results. This means going deeper than just cost savings to understand the full operational impact.
Understanding the Full Value of Preventive Maintenance
Basic ROI calculations focus on repair cost savings, but preventive maintenance offers many additional benefits that are harder to measure. Consistent equipment maintenance leads to better production schedules and higher output. Regular upkeep also means machines run more efficiently, which reduces energy costs and environmental impact.
The financial impact of good maintenance can be significant. One analysis found that preventive maintenance on a 10-year-old air compressor delivered a 545% return on investment. The yearly maintenance costs were much lower than potential repair expenses, showing clear long-term value. Learn more details in this maintenance ROI study.
Communicating Results to Leadership
Getting continued support for preventive maintenance requires showing its worth through clear data. Using charts and graphs helps leaders quickly grasp improvements in key performance indicators (KPIs). Visual presentations make the benefits more obvious and compelling.
Key Performance Metrics to Track
Several important measurements show how well preventive maintenance is working:
- Mean Time Between Failures (MTBF): Tracks average time between equipment breakdowns to show reliability improvements
- Overall Equipment Effectiveness (OEE): Combines availability, performance and quality scores for a complete equipment health view
- Energy Usage: Compares power consumption before and after maintenance to reveal cost savings
- Downtime Reduction: Measures decreases in unexpected equipment outages
Regular tracking of these metrics builds a strong case for preventive maintenance investment. With solid data, maintenance teams can make smarter decisions and improve their programs over time.
Making The Most of Technology For Maintenance Excellence
Technology is essential for making preventive maintenance work well. Having the right tools in place helps maintenance teams spot problems early, fix issues before they cause downtime, and work more efficiently overall.
CMMS: Your Central Information Hub
A Computerized Maintenance Management System (CMMS) provides the foundation for effective preventive maintenance by centralizing all equipment information in one place. Think of it like a digital library containing asset details, maintenance schedules, work orders and parts inventory. Using a CMMS allows teams to automate scheduling, analyze data in real-time, and spend more time on actual maintenance work instead of paperwork.
Smart Sensors and Predictive Analysis
Internet of Things (IoT) sensors take maintenance to new heights by monitoring equipment health in real-time. These sensors track things like temperature, vibration, and pressure - sending data straight to your CMMS. With predictive maintenance, special software analyzes this data to catch potential failures before they happen. It’s similar to a car’s diagnostic system but much more detailed and forward-looking.
Mobile Tools for Field Work
Giving maintenance technicians mobile access to the CMMS means they have critical information at their fingertips. They can instantly receive work orders, check equipment histories, update maintenance records, and find repair guides right from their device. This direct communication reduces time wasted searching for information and helps teams work faster.
Connected Systems Working Together
Getting the most from maintenance technology requires different systems to work seamlessly together. When your CMMS connects with other business software like Enterprise Resource Planning (ERP) systems, it creates a complete view of operations and consistent reporting. For example, linking maintenance data with inventory management enables automatic parts ordering and better stock control.
Making Data Work For You
The information gathered from CMMS, IoT sensors and mobile tools provides valuable insights for improving maintenance practices. Analyzing this data helps identify patterns, predict equipment problems, and optimize maintenance timing. Looking at metrics like mean time between failures shows equipment reliability trends, while reviewing work order history highlights recurring issues. Tools like Auto Service Logger offer specialized vehicle maintenance features that can integrate with your CMMS to capture even more detailed records. This combined data gives a complete picture of asset health, leading to smarter maintenance decisions.
Maximizing Equipment Performance And Longevity
Good equipment maintenance involves much more than basic upkeep. With a well-planned approach to maintenance, companies can keep their assets running efficiently while preventing costly breakdowns. Taking proactive steps helps minimize downtime and get the most value from equipment investments.
Identifying Early Warning Signs
Regular monitoring of equipment condition is essential for catching problems early. Maintenance teams should watch for unusual noises, vibrations, temperature changes, or dips in performance during inspections. Small signs, like increased motor vibration, often signal bigger issues developing. Finding and fixing these warning signs promptly prevents major failures.
Developing Effective Maintenance Schedules
The key is finding the right balance between maintenance costs and equipment reliability. Understanding each asset’s needs and typical failure patterns helps create sensible schedules. Time-based maintenance with regular checkups works well for some equipment. For machines with variable usage, operation-based maintenance triggered by running hours may be better. This focused approach ensures maintenance happens when needed.
The benefits of preventive maintenance are clear - 80% of manufacturing facilities use it to optimize efficiency and reliability. Proper maintenance keeps equipment running smoothly, saves energy, and prevents unexpected failures. Companies see better ROI through less downtime, longer-lasting assets, and more dependable operations. Learn more about the financial impact at Brightly Software’s ROI Guide.
Implementing Condition-Monitoring Practices
Modern condition monitoring takes maintenance further by using sensors and data analysis to track equipment health in real-time. This helps catch developing issues before they become serious problems. Think of it as giving your equipment continuous health checkups.
Adapting Strategies Based on Criticality
Different pieces of equipment need different levels of attention. Critical assets require more frequent inspections and monitoring, while supporting equipment can follow standard maintenance schedules. This helps focus resources where they matter most. Tools like Auto Service Logger help track maintenance needs and monitor equipment condition, especially for vehicle fleets. Having good data leads to smarter maintenance decisions.
Building And Sustaining High-Performance Maintenance Teams
The foundation of any successful preventive maintenance program is a capable and committed team. Creating and sustaining such a team takes careful attention to skill development, clear responsibilities, and ongoing refinement of processes. These elements work together to help your maintenance practices succeed long-term.
Developing Technical Expertise
Building your team’s technical capabilities is essential. Just like athletes who train consistently to stay competitive, maintenance teams need regular skill development to keep their expertise current.
- Cross-Training: Having team members learn multiple equipment types and procedures creates flexibility in scheduling and coverage. When someone is absent, another trained person can step in seamlessly.
- Mentorship Programs: Experienced technicians teaching newer staff helps pass on critical knowledge while creating supportive learning relationships. This direct training speeds up skill acquisition.
- External Training and Certifications: Providing access to specialized courses and certifications shows commitment to professional growth while keeping technical skills fresh.
Fostering Accountability and Ownership
When team members take ownership of their work, quality improves. Set clear expectations and give regular feedback to build accountability.
- Clearly Defined Roles: Each person should understand their specific duties and how their work affects team goals. This clarity helps everyone take responsibility.
- Regular Performance Reviews: Give specific, constructive feedback to help staff improve and recognize good work. This builds open communication.
- Performance-Based Rewards: Consider offering bonuses or recognition programs tied to results to encourage and reward excellent work.
Building a Culture of Continuous Improvement
Top maintenance teams always look for ways to work better. Success comes from learning from both achievements and setbacks.
- Regular Team Meetings: Schedule time to discuss challenges, share what works well, and develop solutions together. This builds collaboration.
- Post-Maintenance Reviews: Check results after maintenance tasks to find potential process improvements. This creates an ongoing feedback cycle.
- New Technology Adoption: Test and implement helpful new tools to improve efficiency. For example, Auto Service Logger can simplify tracking vehicle maintenance and provide useful data.
Maintaining Consistency Across Shifts and Locations
For organizations with multiple shifts or sites, keeping maintenance practices consistent takes extra effort. Clear procedures and communication are key.
- Standard Procedures: Create detailed, step-by-step guides for all maintenance tasks. This ensures quality work regardless of who does it or where.
- Regular Updates: Keep communication flowing between shifts and locations to share tips and lessons learned. This helps maintain consistent practices.
By focusing on skill development, responsibility, and constant improvement, you can build a maintenance team that delivers reliable results. Learn how Auto Service Logger can support your team by making vehicle maintenance tracking simpler and providing data insights.