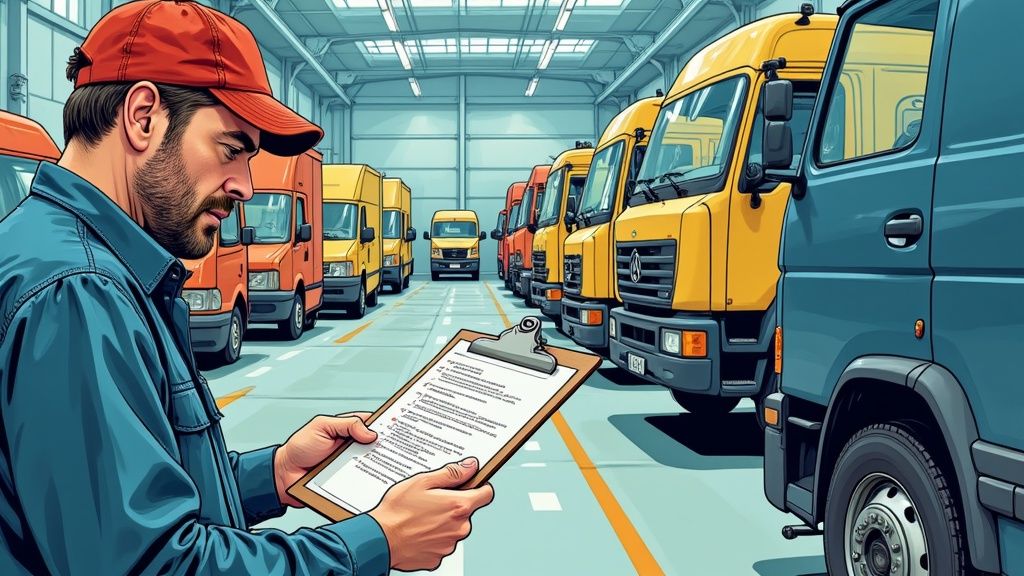
Fleet Vehicle Inspection Checklist: 8-Point Safety Guide
Keeping Your Fleet in Top Shape
Regular vehicle inspections are essential whether you manage a single motorcycle or oversee hundreds of commercial trucks. Vehicle checks have been fundamental since the early days of motorized transport - evolving from basic fluid and tire pressure checks into detailed maintenance systems that match modern automotive technology.
The success of any inspection program depends on being thorough and consistent. Having a detailed checklist and following it carefully can prevent costly breakdowns that lead to unwanted downtime. Regular inspections help ensure safety compliance and protect your valuable vehicle investments from unnecessary wear and damage.
This guide provides an 8-point fleet vehicle inspection checklist covering the most important maintenance areas. We’ll show you how to spot potential issues early, maximize vehicle lifespan, and maintain your entire fleet at peak performance. By following these proven inspection strategies, you can develop an effective maintenance routine that gives you confidence in your fleet’s reliability. The checklist focuses on essential inspection points that matter most for safe, efficient fleet operations.
1. Pre-Trip External Walk-Around
Starting your fleet vehicle inspection with a thorough external walk-around check is essential for safety and maintenance. This quick visual inspection helps spot issues and damage before they become major problems. A proper pre-trip inspection can prevent accidents and costly repairs.
The inspection should check these key areas:
- Body Damage: Check for dents, scratches, rust spots, and document any existing damage. This creates a clear record of the vehicle’s condition.
- Tire Inspection: Examine tire pressure, tread depth, and signs of damage or wear. Good tire maintenance directly impacts safety and fuel costs.
- Light Testing: Check all lights - headlights, taillights, brake lights, turn signals, and hazards. Proper lighting is crucial for visibility and safety.
- Mirror Setup: Position all mirrors correctly to eliminate blind spots and improve driver awareness.
Pre-trip inspections have become standard practice because they work. Consider this real example: A driver skips checking the tires and later has a blowout on the highway, causing delays and expensive roadside service. If found during inspection, that tire could have been replaced safely at the depot.
Benefits:
- Spots problems early
- Creates damage documentation
- Quick to perform
- No special equipment needed
Limitations:
- Won’t catch hidden mechanical issues
- Weather can affect inspection quality
- Good lighting required
Best Practices:
- Use a consistent pattern: Always start at the same spot
- Take photos: Document any damage found
- Carry a flashlight: For better visibility in low light
- Look underneath: Check for fluid leaks
For more vehicle maintenance tips, check out the resources on Auto Service Logger. This site offers helpful information to support your inspection process.
Making the pre-trip walk-around a required part of your inspection routine helps prevent problems, reduces costs, and keeps your fleet running smoothly. This simple check serves as your first defense against avoidable issues and breakdowns.
2. Fluid Level Inspection
Regular fluid level inspection serves as a key part of vehicle maintenance and fleet vehicle safety checks. This essential task involves systematically checking and recording all critical fluid levels according to manufacturer specifications. When done properly, these basic checks help prevent expensive repairs and keep vehicles running reliably.
Key fluid inspection points include:
- Engine Oil: Use the dipstick to check both oil level and condition. Oil that appears dark and gritty indicates time for a change.
- Coolant: Check coolant reservoir levels to prevent engine overheating issues.
- Brake Fluid: Monitor the master cylinder fluid level carefully - low brake fluid creates serious safety risks.
- Power Steering Fluid: Proper fluid levels ensure smooth steering and help spot system leaks early.
- Windshield Washer Fluid: Keep washer fluid topped off for clear visibility in all weather conditions.
A complete fluid inspection covers: measuring oil with the dipstick, checking coolant levels, inspecting the brake master cylinder, and examining all systems for leaks while verifying proper fluid quantities.
Fleet impact example: A delivery company with multiple vans can face major disruptions if even one vehicle has engine problems from low oil. This leads directly to missed deliveries and unhappy customers. Finding small issues early through regular checks prevents bigger problems - like catching a minor power steering leak before it damages the entire pump.
Pros:
- Protects Engines: Proper oil and coolant levels keep engines healthy
- Spots Problems Early: Regular checks catch leaks before major failures
- Easy to Do: Basic fluid checks need minimal tools and training
Cons:
- Can Get Messy: Fluid checks often involve drips and spills
- Timing Matters: Some fluids must be checked when engine is cold
- Waste Disposal: Used fluids require proper environmental handling
Practical Tips:
- Check cold engines: Get the most accurate readings and stay safe
- Use clean rags: Ensure accurate dipstick readings without contamination
- Track all additions: Monitor fluid use to spot developing issues
- Watch for changes: Note unusual colors or smells that may signal problems
This inspection step deserves priority because it directly impacts vehicle reliability, operating costs, and driver safety. While basic, these checks prevent serious mechanical issues when done consistently. This is especially important for fleet vehicles where downtime means lost business. The same careful attention applies to motorcycles, which can be even more sensitive to fluid level problems.
3. Brake System Evaluation
Regular brake system evaluation is essential for keeping fleet vehicles safe and operating efficiently. This inspection looks at key components like brake pads, rotors, and lines while testing overall brake performance to prevent potential safety issues and expensive repairs.
The Role of Brakes in Fleet Safety:
The braking system is the most critical safety component in any vehicle. Properly working brakes protect drivers, other motorists, and pedestrians while helping avoid costly damage. Fleet vehicles need more frequent brake inspections since they rack up high mileage.
What a Complete Brake Inspection Covers:
- Brake Pad Measurements: Check remaining pad material thickness. Thin pads reduce stopping power and can damage rotors.
- Rotor Health Check: Look for warping, grooves, or excessive wear. Bad rotors lead to vibration, poor braking, and faster pad wear.
- Brake Line Assessment: Inspect lines for cracks, leaks, or damage that could cause brake failure.
- Parking Brake Test: Verify proper engagement to prevent vehicle roll-away incidents.
Benefits:
- Safety First: Working brakes are fundamental for accident prevention
- Cost Control: Early issue detection prevents more expensive repairs later
- Legal Requirements: Regular inspections help meet commercial vehicle regulations
Challenges:
- Time Investment: Thorough inspections take dedicated time
- Equipment Needs: Vehicle lifts often required for proper access
- Technical Skills: Accurate diagnosis requires training and expertise
Real Example:
Consider a delivery truck with worn brake pads encountering a sudden road hazard. The degraded brakes fail to stop in time, causing a collision. This shows why consistent brake evaluations matter for preventing accidents and protecting both drivers and the public.
Industry Changes:
Brake systems have evolved from basic drums to complex anti-lock systems (ABS). This advancement, combined with stricter safety rules, highlights why specialized inspection procedures are crucial.
Key Inspection Tips:
- Monitor sounds: Watch for squealing, grinding, or clicking noises
- Check wear patterns: Uneven pad wear may indicate caliper problems
- Test pedal feel: Soft or spongy pedals suggest air in lines
- Inspect fluid: Dark or contaminated fluid needs replacement
Regular brake system evaluation helps fleet managers improve safety, reduce downtime, and control costs. This preventive approach is vital for responsible fleet operations and safer roads for everyone.
4. Tire and Wheel Inspection
Regular tire and wheel inspections are essential for keeping fleet vehicles safe and efficient. These checks require a detailed look at tire condition, pressure levels, wear patterns, and wheel integrity. Making these inspections a priority helps prevent accidents, reduces fuel costs, and extends tire life.
Key Safety and Performance Factors
Your tires affect every aspect of vehicle performance - from handling and braking to fuel consumption. When tires are worn or underinflated, the engine works harder and uses more fuel. Poor tire condition also reduces grip, which is especially dangerous in bad weather. Even minor wheel damage can potentially lead to dangerous tire failures.
Modern Inspection Methods
Basic tire checks have evolved into comprehensive inspections thanks to new tools and techniques. Digital pressure gauges and tread depth meters now provide precise measurements. Regular inspections have become standard practice as fleet managers focus more on preventing problems before they occur.
Essential Inspection Steps:
- Check Tire Pressure: Use quality pressure gauges to verify inflation matches manufacturer specs listed in the vehicle manual or doorjamb
- Measure Tread Depth: Check remaining tread with proper tools - insufficient depth increases skidding risk
- Look for Uneven Wear: Irregular wear patterns often signal alignment or suspension issues that need fixing
- Verify Lug Nut Torque: Ensure wheel nuts are tightened correctly to prevent wheels from coming loose
Benefits:
- Lower Fuel Costs: Proper tire inflation reduces resistance and improves gas mileage
- Longer Tire Life: Finding and fixing problems early helps tires last longer
- Better Safety: Good tire maintenance means better vehicle control and shorter stopping distances
Challenges:
- Frequent Monitoring Required: Tire conditions change regularly and need consistent checking
- Temperature Effects: Hot and cold weather can alter pressure readings
- Equipment Needed: Accurate inspections require specific measuring tools and gauges
Tips for Success:
- Use Quality Tools: Invest in reliable pressure gauges for accurate readings
- Check Cold Tires: Measure pressure before driving when tires are cold
- Track Measurements: Keep records of tread wear to plan replacements
- Visual Inspection: Look for nails, cuts or objects stuck in tires
Success Story: After implementing strict tire inspection protocols, a delivery company significantly reduced both fuel usage and tire-related breakdowns. This led to major cost savings and fewer service interruptions.
Regular tire and wheel inspections help catch problems early, improve safety, and reduce operating costs. Making these checks part of your standard maintenance routine is key for running an efficient fleet operation.
5. Electrical System Check
A working electrical system keeps fleet vehicles running smoothly and safely. Regular checks help prevent unexpected breakdowns and costly repairs. Inspections need to cover all key components including the battery, alternator, lights, and accessories.
Essential Components of an Electrical System Check:
- Battery Testing: Regular load tests show if the battery can hold a proper charge and identify potential issues early
- Alternator Performance: Testing ensures proper charging output and stable power supply to all systems
- Light Inspection: Checking all lights - headlights, taillights, brake lights, turn signals and hazards for safety compliance
- Fuse Examination: Looking for blown fuses that could disable important electrical systems
The Impact on Fleet Operations:
Poor electrical systems directly affect vehicle reliability and safety. For example, a delivery van with a failing battery could leave a driver stranded mid-route, delaying deliveries and requiring expensive roadside service. Basic testing during regular maintenance helps avoid these situations.
Benefits:
- No Surprise Breakdowns: Finding weak batteries or alternator problems before failures keeps vehicles moving
- Legal Compliance: Working lights meet road safety requirements and regulations
- Extended Battery Life: Proper charging prevents premature battery wear
Challenges:
- Equipment Needs: Quality testing requires proper diagnostic tools and meters
- Skill Requirements: Accurate testing and diagnosis needs trained technicians
- Added Inspection Time: Thorough electrical checks extend service appointments
Best Practices for Implementation:
- Clean Connections: Remove corrosion from battery terminals and apply protectant grease
- Complete Light Check: Test every light including interior dome lights
- Running Tests: Check alternator output with engine running
- Monitor Warning Signs: Note any electrical warning lights on dashboard
Modern vehicles rely heavily on electrical systems for basic operation and safety features. From fuel injection to anti-lock brakes, a strong electrical foundation keeps critical systems working properly. Regular testing is key for any fleet - whether cars, trucks or other vehicles.
6. Safety Equipment Verification
Safety equipment checks are a fundamental part of any fleet vehicle inspection checklist. This critical inspection helps protect drivers, passengers, and the public while ensuring compliance with regulations. A thorough verification process examines the condition and functionality of all required safety items.
Key areas to inspect include:
-
First Aid Kit Status: Check for complete and unexpired supplies. A properly stocked first aid kit enables immediate care for minor injuries before medical help arrives. Regular inventory checks help identify missing or damaged items.
-
Fire Extinguisher Readiness: Verify proper pressure levels and inspect for physical damage or corrosion. According to NFPA research, well-maintained fire extinguishers help contain vehicle fires early, preventing major damage and injuries.
-
Emergency Triangle Set: Check that triangles are easily accessible and in good working condition. Proper placement of warning triangles is essential during roadside emergencies, especially in poor weather.
-
Seatbelt Operation: Test each seatbelt’s latching, retraction, and overall condition. Look for fraying, damage, or any issues that could compromise safety during an accident.
Benefits:
- Legal Compliance: Meeting safety equipment requirements helps avoid fines and legal complications
- Emergency Preparedness: Working safety gear helps protect people during accidents or breakdowns
- Simple Process: Safety checks can be completed quickly as part of routine inspections
Challenges:
- Supply Expiration: First aid items and other supplies need regular replacement
- Equipment Security: Safety gear may need protection from theft
- Ongoing Maintenance: Used or damaged items require prompt replacement
Best Practices:
- Monitor Expiration Dates: Check dates on medical supplies and other perishable items
- Keep Equipment Accessible: Store safety gear where drivers can quickly reach it
- Replace Items Quickly: Don’t delay replacing damaged or missing equipment
- Maintain Inventory Records: Keep detailed lists of safety equipment for each vehicle
Safety equipment verification is a key responsibility that helps protect lives and minimize risks. While it may seem like a basic task, having the right safety gear in working order can mean the difference between a minor incident and a serious emergency. Fleet managers who prioritize these inspections demonstrate their commitment to safety while meeting their duty of care obligations.
7. Documentation Review
Documentation review is a key component of fleet vehicle inspections that managers often overlook. This process involves checking registration, insurance, inspection certificates, and maintenance records for each vehicle. When done properly, it helps prevent legal issues, improves maintenance tracking, and makes insurance claims smoother.
Why Documentation Review Matters
While checking physical components like brakes and tires is essential, neglecting paperwork can lead to major problems. If a driver gets stopped with expired insurance, it could result in hefty fines and vehicle downtime. Without organized maintenance records, it becomes difficult to plan repairs and keep vehicles running smoothly.
Key Documentation Areas to Review:
- Expiration Dates: Regular checks of registration, insurance, and inspection certificates help prevent violations and keep vehicles legally compliant
- Maintenance History: Detailed repair records help identify patterns, schedule preventive work, and extend vehicle life
- Accident Reports: Proper documentation of any incidents protects your business during insurance claims and legal proceedings
- Required Permits: Verification of special permits for commercial trucks, hazmat transport, etc. ensures legal operation
Real Examples of Documentation Impact
A trucking company faces steep fines if trucks lack proper interstate permits when crossing state lines. Similarly, a rideshare service without appropriate insurance coverage risks huge liability if accidents occur.
Moving from Paper to Digital
Documentation review used to mean sorting through paper files - time-consuming and prone to errors. Modern fleet management software has simplified this by centralizing digital documents for easy access and verification.
Benefits and Challenges:
Benefits:
- Legal compliance and avoided fines
- Better maintenance tracking and cost control
- Protection during insurance claims
Challenges:
- Paper-heavy without digital systems
- Time-intensive for larger fleets
- Need storage solutions for files
Tips for Better Documentation:
- Use digital tracking systems for streamlined document management
- Set up expiration alerts to prevent missed deadlines
- Keep files organized and easily searchable
- Make copies accessible to authorized staff
Making documentation review a priority in your fleet inspection process helps maintain compliance, optimize maintenance, and protect your business. Though it may seem like busywork, proper documentation plays a vital role in risk management and fleet longevity.
8. Engine Performance Assessment
Checking engine performance is vital for any vehicle fleet inspection. Beyond basic checks like fluid levels, this requires a detailed analysis of how the engine actually runs, including noise levels, output, emissions, and warning signals. Finding issues early helps prevent expensive repairs and breakdowns, while keeping vehicles running efficiently.
Key Components of Engine Performance Checks:
- Cold Start Behavior: Watch how the engine starts from cold. Signs like hard starting, extended cranking or sputtering may indicate ignition problems, fuel system issues or compression concerns.
- Idle Quality: A properly warmed engine should maintain smooth, steady idle. Any roughness, shaking or stalling could mean vacuum leaks, worn spark plugs or sensor problems.
- Exhaust Analysis: Exhaust color tells a story - blue smoke suggests oil burning, white smoke may mean coolant leaks, black smoke often indicates excess fuel use.
- Warning Lights: Take dashboard warning lights seriously. These key indicators need prompt diagnosis with proper testing equipment.
Benefits:
- Early Problem Detection: Finding small issues quickly prevents them from becoming major repairs
- Fewer Breakdowns: Regular checks reduce surprise failures and their costs
- Better Performance: Well-maintained engines deliver optimal fuel economy and power
Limitations:
- Technical Knowledge Required: Full assessment needs mechanical expertise and diagnostic tools
- Some Problems Hard to Find: Subtle performance issues may not be obvious without testing
- Special Tools Needed: While visual checks help, proper diagnosis often requires scan tools
Practical Assessment Tips:
- Monitor Engine Sounds: Note any knocking, ticking or hissing noises that could signal problems
- Track Fuel Usage: Sudden drops in fuel economy may indicate engine issues
- Check Exhaust: Watch for changes from normal clear/light gray exhaust
- Document Changes: Keep records of any shifts in power, idle quality or unusual sounds
Real Example: A fleet manager’s fuel usage tracking revealed higher consumption across multiple vehicles. Engine testing found faulty oxygen sensors causing rich fuel mixtures. Replacing the sensors restored normal efficiency.
As diagnostic tools have advanced, engine performance checks have become more thorough. Fleet operators increasingly see the value of proactive testing for reliability and cost control.
Regular engine performance assessment is essential because the engine is central to vehicle operation. Building this into your maintenance schedule helps ensure reliability while reducing operating costs and downtime. This creates both safer vehicles and better financial outcomes.
8-Step Fleet Inspection Checklist Comparison
Inspection Step | Implementation Complexity 🔄 | Resource Requirements ⚡ | Expected Outcomes 📊 | Ideal Use Cases 💡 | Key Advantages ⭐ |
---|---|---|---|---|---|
Pre-Trip External Walk-Around | Basic, quick visual check | Minimal tools; flashlight optional | Identifies visible damage and safety concerns | Daily pre-trip inspections | Fast, simple, no special tools |
Fluid Level Inspection | Simple but detail-oriented | Dipstick, funnel, clean rags | Prevents engine damage and detects leaks early | Routine maintenance checks | Quick and effective fluid monitoring |
Brake System Evaluation | Involved; may require lift access | Specialized tools and technical know-how | Ensures safety compliance and prevents costly repairs | Critical safety inspections | Comprehensive brake safety verification |
Tire and Wheel Inspection | Moderate; periodic monitoring | Tire pressure gauge, tread depth gauge, torque wrench | Improves fuel efficiency and extends tire life | Regular maintenance and safety checks | Enhances overall vehicle stability and safety |
Electrical System Check | High; requires technical expertise | Multimeter, battery tester, cleaning tools | Prevents starting issues and resolves charging problems | In-depth diagnostic evaluations | Detects hidden electrical faults |
Safety Equipment Verification | Basic checklist procedure | Minimal; visual verification of equipment | Ensures compliance and emergency preparedness | Pre-trip safety verifications | Simple yet vital for regulatory adherence |
Documentation Review | Administrative; paper/digital tracking | Document management software, scanner, filing system | Verifies legal compliance and maintains maintenance records | Regulatory audits and record keeping | Supports insurance claims and legal requirements |
Engine Performance Assessment | Advanced; requires expert evaluation | OBD scanner, engine analyzer, diagnostic software | Detects early engine issues and optimizes performance | Troubleshooting and performance tuning | Early problem detection with detailed insights |
Hit the Road with Confidence
Good fleet vehicle inspections protect your assets and keep drivers safe. By following this 8-point inspection checklist—covering walk-arounds, fluids, brakes, tires, electrical systems, safety gear, paperwork, and engine performance—you’ll extend vehicle life while preventing accidents and expensive repairs.
Make inspections part of your standard processes. Add the checklist to daily and weekly routines so each vehicle gets proper attention. Look carefully for potential issues rather than just going through the motions. Quick identification of problems helps avoid bigger headaches later.
Keep learning and improving your fleet management approach. Stay current on maintenance best practices and safety regulations. Ask drivers to report any concerning vehicle behavior they notice on their routes. Their direct experience helps spot problems early and refines inspection procedures.
Vehicle technology keeps advancing with new developments in electric and autonomous systems. Watch these trends since they’ll shape future inspection needs. Update your checklists as new vehicle types join your fleet to maintain safety and reliability.
Key Takeaways:
- Regular inspections are crucial for fleet safety and longevity.
- Proactive maintenance prevents costly repairs and downtime.
- Driver involvement and feedback are essential for effective inspections.
- Staying updated on industry trends is key for future-proofing your fleet.
Stop wrestling with paper records and upgrade to digital fleet management. Auto Service Logger makes it simple to track maintenance for cars, trucks, and motorcycles. Store complete service histories, monitor mileage, create vehicle reports, and securely save documentation in one central system. The lifetime membership includes custom reporting, dedicated support, and ongoing updates to keep your fleet data organized. Whether you need warranty records, maintenance proof for buyers, or better operational insights, Auto Service Logger puts your fleet’s complete history at your fingertips. Get started today to streamline your fleet management.