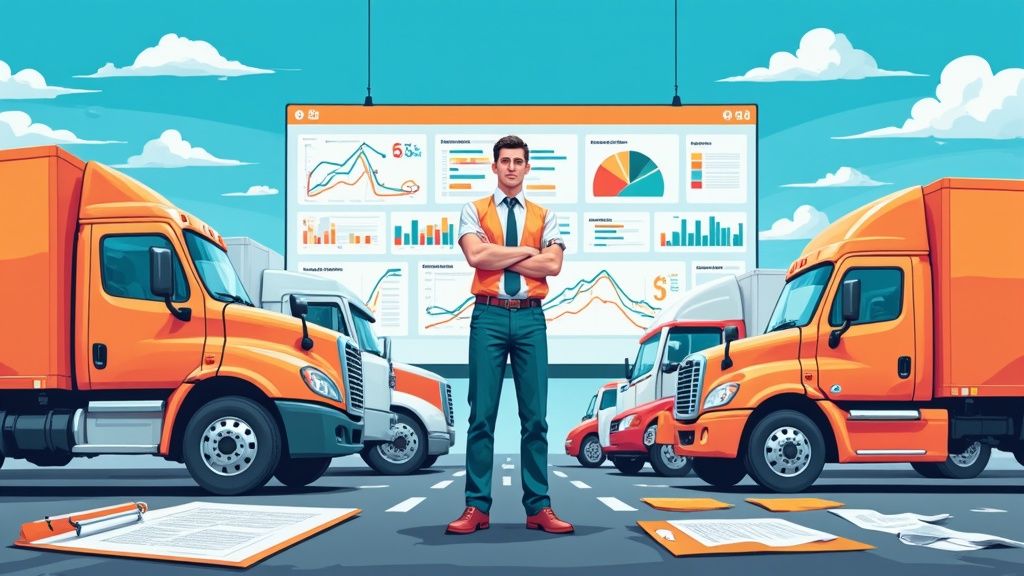
Fleet Management Best Practices: A Field Guide to Operational Excellence
Building Your Fleet Technology Foundation
The key to managing your fleet effectively starts with having the right technology in place. Rather than getting caught up in every new gadget that hits the market, focus on carefully selecting tools that directly address your operational needs and help achieve your business goals. By understanding the core technologies available and how they work together, you can build a system that delivers real results.
Core Technologies for Fleet Management Best Practices
Modern fleet management relies on three essential technologies working in harmony - GPS tracking, telematics, and management software platforms. GPS tracking provides real-time location data that helps optimize routes and dispatch efficiency. Telematics takes monitoring further by collecting detailed information about vehicle performance, driving behaviors, and engine diagnostics. This data flows into fleet management platforms that serve as central hubs for analysis, reporting, and task automation.
For instance, consider how a delivery fleet benefits from this integrated approach. GPS ensures drivers follow optimal routes, while telematics monitors their driving habits and vehicle conditions. The management platform then analyzes all this data to identify opportunities to reduce fuel usage, improve driver training, and schedule preventive maintenance at the right times. This creates an ongoing cycle of measurable improvements.
Choosing the Right Technology for Your Fleet
The key is matching technology to your specific needs. A local delivery service with a few vehicles may only need basic GPS tracking and a simple management platform. In contrast, a nationwide trucking company requires advanced telematics and detailed analytics to effectively manage their larger, more complex operation.
Looking ahead is also critical when selecting technology. Consider whether the system can scale as your business grows and integrate smoothly with your current tools to prevent data silos. For help organizing your fleet information effectively, check out our guide on sitemap structure.
Implementing Technology Effectively: Real-World Examples
Proper planning and execution are essential for successful technology adoption. Two common mistakes are inadequate staff training, which leads to resistance and inaccurate data usage, and failing to establish clear metrics to measure impact. Without specific goals and ways to track progress, it’s impossible to gauge if the technology is truly helping.
Take the example of a fleet that implemented telematics to reduce fuel costs. By training drivers on fuel-efficient techniques and using the system to track fuel consumption, they cut fuel expenses by 15% in six months. Another fleet achieved a 40% reduction in accidents after installing in-cab cameras and using the footage for targeted driver coaching. These examples show how combining the right technology with proper implementation leads to significant, measurable improvements in safety and efficiency.
Crafting Fleet Policies That Actually Work
Good fleet policies are the backbone of successful fleet operations. Rather than being static documents filed away and forgotten, effective policies actively guide daily operations while protecting both assets and drivers. Creating practical, real-world policies requires looking beyond basic vehicle maintenance schedules to address the full scope of fleet management challenges.
Key Components of Effective Fleet Policies
Strong fleet policies need to cover many operational areas - from driver behavior and vehicle maintenance to fuel management and accident procedures. A solid driver policy, for example, clearly outlines expectations around safe driving practices, including specific rules about speed limits, phone use, and required rest periods. Vehicle maintenance policies should detail inspection schedules, preventive maintenance timing, and steps for handling repairs. When well-designed, these policies help reduce risks and keep operations running smoothly.
Fuel management provides another key example. Good policies specify approved fueling locations, explain how to track fuel use, and outline ways to drive more efficiently. This helps control costs while supporting environmental goals. Accident procedures are equally important - clear policies ensure consistent reporting, proper documentation, and quick response times to minimize disruptions.
Implementing and Enforcing Fleet Policies
Writing policies is just the first step - putting them into practice takes careful planning. For policies to work, employees need thorough training through methods like hands-on workshops, online modules, or mentoring from experienced drivers. Regular enforcement combined with recognition for following the rules helps build a culture where safety and accountability matter.
Adapting Policies to Your Needs
One-size-fits-all policies rarely work well. A small local delivery service faces different challenges than a large trucking company, so policies need to match your specific situation. Important factors include fleet size, types of vehicles, and geographic area. Regular policy reviews help ensure guidelines stay current as regulations and technology change.
Maintaining Balance: Compliance and Flexibility
The best fleet policies strike a balance between following rules and allowing reasonable flexibility. While policies must meet legal and safety requirements, they should also empower drivers to make smart decisions in real-world situations. According to Verizon Connect, using telematics improves efficiency by 62% - similarly, well-designed policies boost operational effectiveness when they provide clear guidance while trusting drivers’ judgment. Thoughtful policies, consistently applied, create the foundation for fleet success.
Making Route Optimization Your Competitive Edge
While solid fleet policies create a foundation, the key to truly efficient operations lies in optimizing delivery routes. This involves much more than plotting simple point-to-point paths - it requires strategically planning routes that reduce costs, help drivers work more efficiently, and keep customers satisfied. Fleet managers need to take a flexible, data-driven approach to route planning to achieve these goals.
Balancing Competing Priorities in Route Optimization
Creating optimal routes means juggling multiple important factors. High fuel costs make efficiency critical, but focusing only on the shortest distance can backfire if it means longer travel times that disrupt delivery schedules. Driver wellbeing also matters significantly - routes that look good on paper but create stress through unrealistic timing or constant changes will ultimately hurt both morale and performance. For instance, sending drivers through heavy traffic to save a few miles often wastes more time and fuel while frustrating everyone involved. Success requires carefully weighing all these elements together.
Implementing Route Optimization Tools: Practical Approaches
Modern technology provides excellent solutions for handling these complex routing challenges. Good route optimization systems do far more than basic GPS - they factor in real traffic patterns and can automatically reroute drivers around delays. These tools also track delivery windows and driver hours-of-service limits to maintain both customer satisfaction and regulatory compliance. Many platforms connect with other fleet systems too, creating a central hub for analyzing performance data and making better decisions. This integrated approach helps fleet managers implement more effective routing strategies based on actual results.
Using Data for Continuous Improvement
Smart fleet managers recognize that data insights drive better routing. Historical information reveals important patterns in traffic flow, driver performance, and delivery efficiency that help refine future route planning. Quick adjustments are also essential - road closures, accidents, and schedule changes require rapid route updates to stay on track. Quality routing software enables these real-time changes smoothly. When a driver encounters an unexpected road closure, for example, the system can immediately suggest an alternate route while keeping customers informed about any delays. This combination of data analysis and responsive technology gives fleet operations a real advantage in today’s competitive environment.
Turning Fleet Data Into Action
While optimizing routes and establishing clear fleet policies are crucial, their true value emerges when paired with data-driven decision making. Success in fleet management requires more than just gathering data - it demands careful analysis and concrete actions based on meaningful insights. Understanding which metrics matter most and how to use them effectively is key to improving overall fleet performance.
Identifying Key Performance Indicators (KPIs)
The first essential step is choosing KPIs that directly connect to your business objectives. These metrics need to be both measurable and meaningful. For instance, if reducing fuel expenses is the goal, you’ll want to track fuel usage per mile, idle time, and sudden braking events. When safety is the priority, focus on metrics like speed violations, proper seatbelt use, and close-call incidents. By zeroing in on the right indicators, you can direct your efforts where they’ll have the greatest impact.
Transforming Raw Data into Actionable Insights
Collecting data is just the beginning. To be useful, raw telematics information must be analyzed to uncover important patterns. This is where fleet management software becomes essential. Modern systems can automatically create clear visual reports using charts and graphs that make it easy to spot issues and opportunities. For example, when fuel consumption suddenly rises, it might signal the need for driver coaching on efficient driving habits or point to vehicles requiring maintenance. This approach helps fleet managers move from fixing problems after they occur to preventing them entirely.
Practical Approaches to Data Analysis
You don’t need advanced statistical knowledge to make sense of fleet data. Many fleet management tools offer straightforward dashboards that make analysis simple. These systems let managers filter information by driver, vehicle, or time period to get detailed insights. Setting up automatic alerts for specific events - like exceeding speed limits or entering restricted areas - enables quick responses to potential issues. This way, small problems can be addressed before they become major concerns.
Communicating Data Effectively
Success with data requires clear communication to both drivers and management. Drivers benefit from personal performance reports that show areas for improvement while celebrating their achievements. For executives, focus on summary reports that demonstrate how fleet initiatives impact business goals, such as reduced operating costs or faster delivery times. Tools like Auto Service Logger can help by providing detailed maintenance records, adding to your understanding of overall fleet performance. When you present data in ways that resonate with different audiences, you build support for continued investment in fleet management improvements and create positive change throughout the organization.
Building a Culture of Fleet Safety Excellence
Creating an effective fleet safety program requires more than ticking compliance boxes - it demands building a culture where safe driving becomes second nature. The most successful fleets focus on prevention rather than reaction by combining smart technology use, regular training, and positive reinforcement to create lasting behavioral change.
Integrating Technology for Enhanced Safety
Modern fleet safety relies heavily on technology tools that provide detailed insights into driver behavior. In-cab video systems have proven particularly valuable, with 68% of fleets reporting major safety improvements after implementation. These systems help identify specific risk factors like speeding or sudden braking that require coaching. When paired with GPS tracking and telematics, fleet managers can monitor performance in real-time and quickly address concerning patterns. For instance, if a driver regularly exceeds speed limits, the system alerts managers to have a timely conversation. This creates an ongoing feedback cycle that steadily improves driving habits.
Empowering Drivers Through Effective Coaching
The key to changing behavior is constructive coaching that focuses on growth rather than criticism. Rather than simply pointing out mistakes, effective coaches review incidents with drivers to explore better approaches. For example, after a harsh braking event, reviewing the video footage together helps identify what led to the situation and how to handle it differently next time. This collaborative approach helps drivers understand the “why” behind safety practices and take ownership of their performance. Recognition programs that reward consistent safe driving records provide extra motivation to maintain high standards.
Overcoming Resistance to Safety Initiatives
New safety programs often face initial pushback, especially around increased monitoring. The best way to address these concerns is through open communication about how the programs benefit drivers themselves. This includes explaining how video footage protects drivers in accident investigations and how safer driving leads to lower insurance costs. Getting driver input during program development and implementation is also crucial - when drivers help shape the policies, they’re more likely to support them. Regular feedback sessions where drivers can voice concerns and suggest improvements help maintain buy-in over time.
Measuring the Impact of Safety Programs
Tracking clear metrics is essential for evaluating and improving safety initiatives. Key performance indicators like accident rates, near misses, and violations show whether programs are working as intended. Regular review of these metrics helps identify gaps that need attention. For instance, if collision rates don’t improve after new training, the program may need adjustments. This data-driven approach, combined with strong driver engagement and smart technology use, creates lasting safety improvements that benefit both drivers and the organization. The focus should remain on continuous refinement based on real results.
Measuring What Really Matters in Fleet Performance
Fleet managers rely on specific metrics and key performance indicators (KPIs) to assess their operations, much like doctors use vital signs to monitor patient health. Having a clear understanding of which metrics matter most helps managers make data-driven decisions that improve efficiency and bottom-line results.
Identifying Key Performance Indicators (KPIs) for Fleet Management Best Practices
Choosing relevant KPIs is essential for focusing efforts on areas that deliver the most value. The specific metrics to track depend on your business goals - a long-haul trucking company might focus on fuel efficiency and driver hours, while a local delivery service likely prioritizes on-time delivery rates and vehicle usage.
For example, a trucking company focused on controlling fuel costs would track:
- Fuel Consumption per Mile: This shows driving efficiency and maintenance needs
- Idle Time: Helps identify wasted fuel and unnecessary engine wear
- Average Speed: Monitoring speed helps optimize fuel economy within legal limits
Meanwhile, a delivery service centered on customer satisfaction might focus on:
- On-Time Delivery Rate: Direct measure of service quality
- Number of Deliveries per Route: Shows route and driver productivity
- Customer Feedback Ratings: Provides insights into service quality
Turning Data Insights into Actionable Strategies
Once you identify your key metrics, the next step is converting raw data into clear action items. This is where [fleet management software] plays an essential role - automatically generating reports, displaying trends visually, and alerting managers to issues needing attention.
For instance, if fuel consumption suddenly increases, the system can notify managers to investigate potential causes like needed vehicle maintenance or opportunities for driver coaching. This allows for proactive problem-solving rather than just reacting to issues after they occur.
Using Data to Drive Continuous Improvement in Your Fleet
Analyzing fleet data should be an ongoing process, not a one-time task. Regular KPI reviews and adjustments based on trends help drive sustained improvements. Just as a gardener constantly monitors plants and adjusts care based on their needs, fleet managers should continuously track metrics and refine strategies accordingly.
Take the example of analyzing historical delivery times and traffic patterns to identify consistently delayed routes. This insight could prompt route changes, adjusted delivery windows, or staff schedule updates. Through this cycle of measuring, adjusting, and measuring again, fleets can steadily enhance their performance over time.
Ready to improve your fleet operations? Explore how Auto Service Logger can help implement these practices and maximize your fleet’s potential. From comprehensive maintenance records to customizable reporting, Auto Service Logger provides the tools needed to track what matters and drive success.