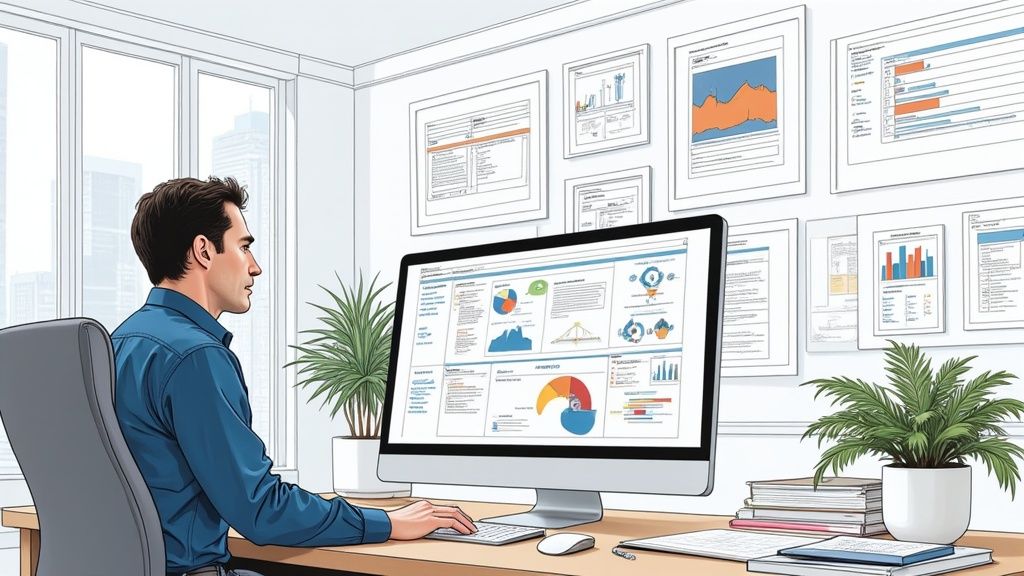
Fleet Maintenance Software: A Practical Guide to Transforming Your Operations
Breaking Down Modern Fleet Maintenance Solutions
Fleet maintenance has evolved far beyond basic record-keeping in logbooks and spreadsheets. Smart software now helps fleet managers boost efficiency and cut costs while keeping vehicles running smoothly. As companies focus more on maximizing vehicle uptime, the fleet maintenance software market is expected to grow to $14.08 billion by 2031.
The Power of Predictive Maintenance
Modern fleet software doesn’t just track repairs - it helps prevent problems before they happen. Similar to how doctors use health histories to assess disease risk, maintenance programs analyze data from vehicle sensors and past repairs to spot potential issues early. For example, systems like Fleetio use real-time telematics data to predict when components might fail. This means fleets can schedule maintenance at convenient times rather than dealing with sudden breakdowns that hurt productivity and profits.
Embracing Cloud-Based Solutions
Cloud technology has changed how fleet managers work with maintenance data. With cloud-based systems, managers can check reports, track driver behavior, and update maintenance schedules from any device with internet access. Programs like Auto Service Logger eliminate the need for expensive servers and IT staff. This makes them great for companies that want flexible, cost-effective ways to manage their fleets.
Addressing the Electric Vehicle Revolution
The rise of electric vehicles brings new challenges for fleet maintenance. Traditional service plans don’t cover EV-specific needs like battery health monitoring and charging management. As more companies add EVs to meet regulations like the EU’s 37.5% emissions reduction target by 2030, maintenance software is adapting to handle both conventional and electric vehicles. This shift shows how fleet software continues to grow alongside industry changes.
Overcoming Implementation Challenges
While adopting new software takes work, good planning makes the process smoother. Success starts with getting everyone on board - from drivers to executives. Clear communication about benefits and thorough training help teams embrace the change. Choosing software that works well with existing systems also makes the transition easier. When companies tackle these challenges directly, they can get the most value from their fleet maintenance software and see real improvements in their operations.
Making Data Work for Your Fleet
Managing a modern fleet requires more than basic vehicle maintenance - it demands making sense of the extensive data generated during daily operations. Smart fleet managers are moving away from simply fixing problems after they occur and instead using data analysis to prevent issues before they happen. Quality fleet maintenance software makes this proactive approach possible.
From Reactive to Proactive: The Power of Predictive Analytics
By analyzing maintenance records, real-time vehicle data, and external factors like weather conditions, fleet managers can spot potential problems early. For example, when a delivery company notices their vehicles experience more tire wear on certain routes during hot weather, they can use fleet software to predict exactly when those tires will need replacement. This prevents breakdowns, reduces repair costs, and keeps vehicles running longer.
Identifying Early Warning Signs
One significant benefit of data-driven maintenance is the ability to identify minor issues before they escalate into serious problems. Fleet managers have access to tools like Auto Service Logger that allow them to track essential metrics, including fuel consumption, engine operating hours, and mileage. Unanticipated changes in these metrics can often indicate emerging mechanical issues. This proactive approach ensures that problems such as worn brake pads are addressed during routine maintenance, reducing the risk of emergency repairs.
Optimizing Service Schedules
Smart data analysis helps fleet managers schedule maintenance at exactly the right time. By tracking each vehicle’s maintenance history and usage patterns, fleet software can determine the best intervals for preventive service. This prevents both unnecessary early maintenance and dangerous delays. Managers can also schedule work during off-peak hours or combine multiple services into single appointments to minimize disruption.
Tailoring Strategies to Your Fleet
Different fleets have different needs - a local delivery service faces very different challenges than a cross-country trucking company. Fleet maintenance software provides detailed data specific to your operation’s size and vehicle types. This allows you to create custom maintenance plans that focus on your fleet’s actual needs, whether that’s improving fuel efficiency, reducing wear on specific parts, or meeting industry regulations. The key is using data to build a practical maintenance strategy that works for your specific situation.
Cloud Solutions That Actually Deliver
Moving fleet maintenance software to the cloud has fundamentally changed how fleets operate. The shift brings concrete advantages - from anywhere access to lower costs to smarter planning. When organizations adopt cloud systems, they gain tools to meet their current and future needs more effectively. The growing market for these platforms, expected to reach $14.08 billion by 2031, shows just how essential they’ve become.
Accessibility and Real-time Insights
The ability to access data from anywhere is a key strength of cloud platforms like Auto Service Logger. Gone are the days of information trapped on a single office computer. Now, team members can tap into critical details whether they’re at headquarters, working remotely, or on the road. This instant access means faster responses when issues arise. For example, if a driver encounters mechanical problems far from base, they can immediately alert the maintenance team. Technicians can then assess the situation remotely and guide needed repairs, keeping vehicles moving and drivers safe.
Cost Savings and Efficiency
Cloud solutions help organizations save money in several ways. They eliminate the need for extensive IT infrastructure since providers handle servers and updates. The software also automates many administrative tasks, freeing up staff time for more valuable work. Instead of managing complex systems, teams can focus on core activities like preventive maintenance and driver training. This shift often means companies can redirect IT resources to areas that directly impact their bottom line.
Data-Driven Decisions and Predictive Maintenance
Cloud platforms make it easier to use data for smarter fleet management decisions. By gathering all maintenance records in one place, managers gain clear insights into how their fleet is performing. This helps them spot trends, improve maintenance timing, and solve problems before they grow. The software can even predict potential breakdowns by analyzing past repairs and real-time vehicle data. This proactive approach reduces repair costs and keeps vehicles on the road longer. It’s no wonder that over 40% of fleet managers now use cloud platforms to work more efficiently and stay ahead of maintenance needs.
Mastering Electric Vehicle Fleet Management
Electric vehicles are becoming a standard choice for business fleets, bringing new considerations for maintenance and management. While traditional vehicles focus on oil changes and engine care, EVs require a different approach centered on battery health, charging systems, and electric motor maintenance. For fleet managers, this means adopting new tools and strategies to keep their vehicles running efficiently.
Key Differences in EV Fleet Maintenance
The basic idea of preventive maintenance remains important, but EVs bring specific needs. Battery monitoring becomes essential - tracking charge cycles, temperature patterns, and overall capacity helps maintain peak performance. Tires also need more attention in EVs since the extra weight and instant torque lead to faster wear. Electric motors, though reliable, require specialized diagnostic tools and maintenance procedures that differ from standard engines. These unique needs highlight why specialized fleet management software is crucial for EV fleets.
Using Fleet Maintenance Software for EV Management
Modern software solutions like Auto Service Logger offer features designed specifically for EV fleets. For instance, these systems can track charging patterns, manage energy use, and help schedule charging during off-peak hours to reduce costs. The software analyzes battery data to spot potential issues early, helping extend battery life and reduce unexpected problems. It also helps schedule routine maintenance for key components like tires, brakes and motors, keeping vehicles on the road longer.
Building a Sustainable EV Maintenance Program
Creating an effective EV fleet program requires careful planning beyond just buying electric vehicles. Technicians need proper training to handle high-voltage systems and understand EV-specific maintenance needs. Managing charging infrastructure becomes part of daily operations - from monitoring charger status to coordinating energy use across the fleet. Choosing the right management software ties everything together, offering a clear view of both electric and traditional vehicles in one system. By addressing these key areas, businesses can develop maintenance programs that keep their EVs running reliably while controlling costs. With the fleet maintenance software market expected to reach $14.08 billion by 2031, having strong EV management capabilities will help determine which fleet operations succeed.
Navigating Global Fleet Management Trends
Managing fleet vehicles effectively has become more complex as economic changes, growing cities, and e-commerce reshape how organizations maintain vehicles across different regions. Smart fleet maintenance strategies are more important than ever, with the fleet maintenance software market set to reach $14.08 billion by 2031.
Regional Differences in Maintenance Approaches
Local conditions create distinct fleet maintenance needs across regions. For instance, busy cities with good public transit tend to use smaller, efficient vehicles and outside maintenance services. Meanwhile, rural areas often rely on larger trucks for long-distance transport and maintain their own service facilities. Areas with developing economies may have limited access to skilled technicians and modern tools, affecting their maintenance options. These differences highlight why flexible fleet maintenance software matters.
The Impact of E-commerce and Urbanization
E-commerce growth means delivery fleets need more frequent maintenance and faster repairs to keep vehicles running. This is especially true in cities where quick deliveries are essential, putting extra wear on vehicles and requiring careful maintenance planning. Quality fleet maintenance software helps by tracking vehicle health, scheduling preventive work, and finding efficient delivery routes to reduce downtime. The shift toward electric vehicles in cities also brings new maintenance requirements.
Adapting to Local Needs While Maintaining Global Standards
Companies with international fleets must balance meeting local rules while keeping consistent standards worldwide. Rules about emissions, vehicle checks, and driver time limits vary between countries. Tools like Auto Service Logger help track these different requirements and ensure both local compliance and consistent maintenance across the whole fleet. This approach reduces legal risks and saves money by standardizing work where possible.
Learning from Global Best Practices
Studying successful international fleet operations provides valuable lessons for improving maintenance programs. Leading companies often use central fleet maintenance software to monitor all their vehicles, no matter where they operate. They also focus on training drivers and sharing information between regions to keep maintenance practices consistent. By understanding what works for others and how factors like economic growth and city development affect maintenance needs, you can build a more effective fleet program that adapts well to change.
Making Implementation Work
Fleet maintenance software success depends on more than selecting the right product. To get real value from your investment, you need a clear plan for managing change, driving adoption, and making the software an essential part of your daily operations. Without proper planning, implementation can fail to deliver results and leave teams frustrated. Here’s how to make it work.
Building a Foundation for Success
Start by laying strong groundwork. Define specific goals for what you want the software to help you achieve - whether that’s less vehicle downtime, better maintenance scheduling, or tighter control over fuel expenses. These concrete objectives will help you measure progress and success.
Put together a diverse implementation team that includes people from maintenance, operations, and IT departments. Having different perspectives helps identify potential issues early and creates champions who can promote the software throughout your organization. This team will guide the rollout and help overcome any challenges that arise.
Choosing the Right Fleet Maintenance Software
When selecting software, the decision significantly impacts your operations. Consider crucial elements such as the size of your fleet, the variety of vehicle types you manage, and any unique maintenance requirements you have. It’s essential that the software is compatible with the specific demands of your industry and can integrate seamlessly with existing tools, such as telematics systems or fuel card services. Dedicate ample time to carefully assess the available options and choose a software solution that supports your strategic objectives over an extended period.
Driving User Adoption
People often resist new systems and processes. Counter this by clearly showing your team how the software will benefit their daily work. Show them how it simplifies tasks and increases efficiency. Provide thorough training through different formats - online guides, hands-on practice sessions, and real-time support. When people understand the software and feel confident using it, they’re much more likely to embrace it.
Measuring Implementation Success
Track important metrics to see if implementation is working. Look at things like how many people actively use the system, how accurate the data is, and whether you’re meeting your original goals. For example, if you wanted to reduce breakdowns, compare those numbers before and after using the software. Review metrics regularly with your team and adjust your approach based on what’s working. This keeps you focused on getting maximum value from your investment.
Remember that good implementation is ongoing, not just a one-time project. Following these guidelines helps ensure smooth adoption and lasting benefits from your fleet maintenance software. Ready to improve your fleet operations? Learn more about how Auto Service Logger can help achieve your maintenance goals.