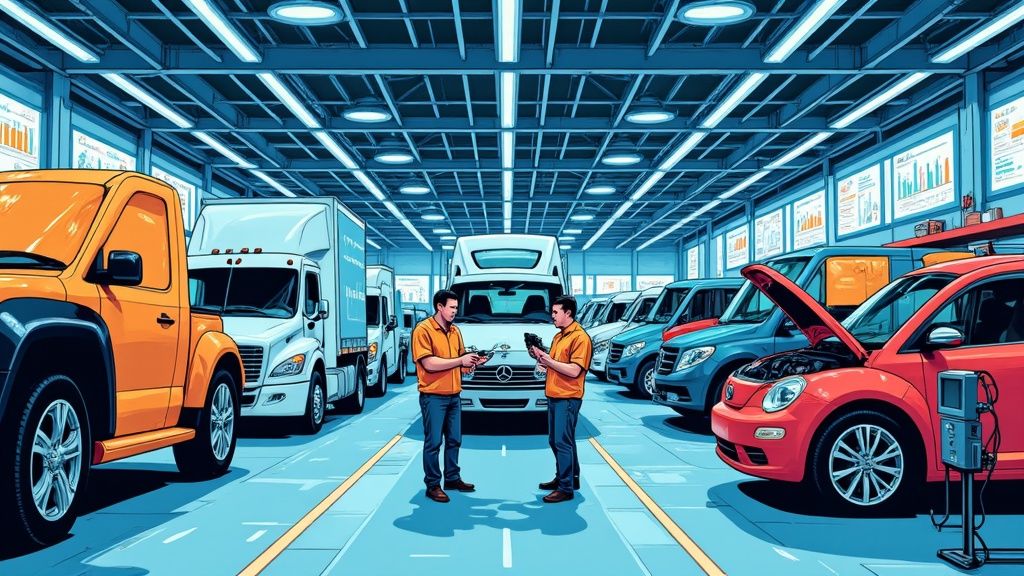
Fleet Maintenance Mastery: Transform Your Vehicle Management Strategy
Navigating Fleet Maintenance Challenges
Maintaining fleet vehicles has become increasingly challenging in today’s economy. Fleet managers face mounting pressure from repair costs that rose up to 20% in early 2023, while supply chain disruptions create ongoing parts shortages. With older vehicles being kept in service longer out of necessity, the need for smart maintenance strategies has never been more important. These compounding factors require fleet managers to take a more strategic approach to keeping vehicles running efficiently while controlling costs.
Addressing Rising Repair Costs
The dramatic increase in repair expenses presents a major hurdle for fleet operations. Parts shortages and delivery delays drive up costs, while industry-wide labor shortages mean higher service rates at repair facilities. To combat these rising expenses, many fleet managers are strengthening their preventive maintenance programs. By catching and fixing small issues early, they can avoid more expensive repairs down the road. This proactive stance helps control costs while maximizing vehicle uptime.
Managing Parts and Inventory Effectively
Smart parts management is essential given today’s unpredictable supply chains. While maintaining adequate parts inventory is important, simply stockpiling items isn’t the answer. The key is using data analysis to predict which parts will be needed and optimizing stock levels accordingly. This helps prevent both stockouts and excess inventory costs. Building strong supplier relationships also becomes crucial - reliable partners who can provide consistent parts availability and competitive pricing help minimize the impact of supply chain disruptions.
The Impact of Extended Vehicle Lifecycles
With new vehicle acquisitions still difficult, many fleets must extend the service life of their existing vehicles. While this reduces immediate capital costs, it creates maintenance challenges as older vehicles typically need more frequent repairs. Success requires shifting to predictive maintenance strategies powered by vehicle data and monitoring. This allows teams to spot developing issues before they cause breakdowns. Tools like Auto Service Logger help track maintenance history and costs, enabling smarter decisions about when to repair versus replace aging assets.
Embracing Technology for Proactive Maintenance
Technology is becoming essential for effective fleet maintenance. Modern telematics systems monitor vehicle performance in real-time, alerting managers to potential problems before they cause failures. This data-driven approach helps optimize maintenance scheduling and reduce unexpected downtime. Fleet maintenance software centralizes information, improves communication between teams, and provides analytics to guide decisions. When used effectively, these technological tools help fleet managers control costs while keeping vehicles reliable and ready for service.
Building a Preventive Maintenance Powerhouse
Having an effective preventive maintenance (PM) program is essential for every successful fleet operation. Rather than constantly dealing with unexpected repairs and their associated costs, a well-designed PM program helps you stay ahead of issues through systematic, proactive vehicle care. When implemented properly, preventive maintenance becomes part of your organization’s culture and leads directly to longer vehicle life and less downtime.
Designing a Maintenance Schedule That Works
The foundation of effective preventive maintenance is creating customized maintenance schedules based on each vehicle’s specific needs. Consider key factors like vehicle type, age, mileage, and typical usage patterns. For example, a delivery truck making frequent stops in city traffic needs different maintenance intervals than a sales vehicle used mainly for highway driving. Environmental conditions also play a major role - vehicles operating in extreme temperatures or rough terrain require more frequent service. This detailed approach ensures every vehicle gets exactly the maintenance it needs at the right time.
The Power of Proactive Inspections
Regular inspections are critical for catching small issues before they become major problems. Think of these inspections as health check-ups that keep your fleet in top condition. A complete inspection should examine everything from basic items like tire pressure and fluid levels to more complex systems like brakes and electrical components. Beyond preventing breakdowns, these inspections generate valuable data about vehicle health trends over time. Tools like Auto Service Logger help track and analyze this inspection history, making it easier to spot patterns and adjust maintenance plans accordingly.
Leveraging Telematics for Predictive Maintenance
Modern fleet management now has access to real-time vehicle data through telematics systems, taking maintenance from reactive to truly predictive. These systems continuously monitor key vehicle metrics, letting you address potential issues before they cause breakdowns. For example, tracking engine temperature and oil pressure patterns can reveal emerging problems that would otherwise go unnoticed until failure. This data-driven approach helps you schedule maintenance more strategically and allocate resources more efficiently. By combining telematics insights with your inspection records and maintenance schedules, you create a comprehensive system that maximizes vehicle uptime while minimizing repair costs. The result is a more reliable fleet that delivers consistent performance while staying within budget.
Mastering the Economics of Fleet Repair
Managing fleet maintenance costs effectively requires more than just reducing expenses - it demands a thoughtful strategy that balances cost control with maintaining high service quality. To achieve this balance, fleet managers need to carefully evaluate several key areas of their maintenance programs.
Strategic Partnerships and Negotiation
Building strong relationships with service providers creates opportunities for mutual benefit. By establishing preferred vendor agreements, fleets can secure better rates on parts and labor based on volume commitments. Regular communication with repair shops also helps streamline diagnosis and repair processes, reducing vehicle downtime. For example, when shops understand your fleet’s specific needs and priorities, they can fast-track critical repairs and suggest preventive measures that save money long-term.
Smart Inventory Management
Getting parts inventory right directly impacts your bottom line. Too much stock ties up capital and risks parts becoming obsolete, while too little leads to costly delays. The solution lies in data-driven management. Much like grocery stores track product demand, fleet managers should analyze repair history and expected maintenance needs to determine optimal stock levels. This approach ensures you have critical parts available without excess inventory costs. Auto Service Logger and similar tools can help track usage patterns and generate reports to guide inventory decisions.
In-House vs. Outsourced Maintenance: A Data-Driven Decision
Deciding between in-house maintenance and outsourcing requires careful analysis of your fleet’s specific situation. Key factors include fleet size, repair complexity, and local labor availability. A large fleet with specialized equipment might benefit from dedicated in-house technicians, while smaller operations often find outsourcing more cost-effective. The decision should be based on concrete data - compare current maintenance costs, labor rates, and potential ROI of establishing in-house facilities to determine the best path forward.
Optimizing Labor and Procurement
Labor typically represents one of the largest portions of maintenance expenses. Improving efficiency here starts with smart scheduling and cross-training technicians to handle various repair types. On the procurement side, establishing strong supplier relationships and using systems to automate parts ordering helps reduce costs and prevent delays. For instance, scheduling routine maintenance during slower periods and training technicians on multiple vehicle types can maximize productivity. The key is continuous evaluation and refinement of these processes, always looking for ways to reduce waste while maintaining high service standards. This ongoing commitment to improvement helps ensure your fleet maintenance program delivers value while keeping vehicles safe and reliable.
Transitioning to Electric Vehicle Maintenance
More fleets are adopting electric vehicles (EVs), creating new opportunities and challenges for maintenance teams. While EVs can reduce long-term costs through lower fuel usage and simpler powertrains, they require different maintenance approaches than traditional vehicles. Making this shift successfully requires careful planning around technician skills, facility updates, and component care.
Rethinking Technician Training
Working on EVs demands a completely different skillset compared to combustion engines. Technicians need specific training to safely handle high-voltage systems and use specialized diagnostic tools for electrical troubleshooting. For instance, techs must learn proper safety protocols for working with high-voltage components and master new diagnostic software for EVs. This focused training protects both technicians and vehicles while ensuring optimal fleet performance.
Adapting Maintenance Facilities
Adding EVs to a fleet means modifying maintenance facilities to support them properly. This includes installing charging stations, creating dedicated high-voltage work areas, and acquiring EV-specific tools and equipment. For example, shops need insulated tools for electrical work and proper battery storage areas to meet safety requirements. Without these essential facility updates, maintaining EVs safely and efficiently becomes much more difficult.
Managing Unique EV Components
EVs contain specialized parts like battery packs and electric motors that require different care than traditional vehicle components. Proper maintenance involves regular battery health monitoring, thermal management system checks, and detailed component inspections. Battery packs need ongoing evaluation for degradation and temperature imbalances, while electric motors require periodic lubrication and wear checks. Understanding these maintenance differences is key for keeping EVs running reliably.
Optimizing Mixed Fleet Maintenance
Many organizations now operate both electric and traditional vehicles, creating more complex maintenance needs. Successfully managing different service schedules, parts inventories, and technician training across vehicle types takes careful coordination. Fleet managers can use tools like Auto Service Logger to track maintenance timing, manage parts stock, and analyze data for both vehicle types. This helps create an organized approach that keeps the entire fleet healthy while smoothly incorporating EVs over time.
Maximizing Vehicle Lifecycle Value
Running a successful fleet operation hinges on making smart decisions about each vehicle’s entire service life. Fleet managers must carefully consider when to invest in repairs and when replacement makes more sense financially. By taking a data-focused approach to these decisions, you can optimize your fleet’s value over time.
Evaluating Vehicle Performance and Predicting Costs
Getting the most value from your fleet starts with thorough performance tracking. This means going beyond basic metrics like mileage and fuel usage to monitor repair frequency, downtime periods, and total operating expenses. For instance, if a vehicle needs increasingly frequent repairs despite regular maintenance, it may be reaching the end of its cost-effective life. Tools like Auto Service Logger help track this data so you can spot trends and plan for future maintenance needs. By building this detailed performance history, you can better anticipate costs and adjust your budget accordingly.
The Art of Vehicle Cycling Strategies
Once you have good data on maintenance patterns, you can make smarter decisions about vehicle replacement timing. The key is finding the sweet spot where the cost of keeping an aging vehicle running exceeds the expense of replacing it. Think of it like maintaining any equipment - at some point, constant repairs become more expensive than investing in new equipment that will run more reliably. Knowing when to make this switch keeps your fleet running efficiently while controlling costs.
Data-Driven Decisions for Fleet Renewal
Smart fleet renewal relies on careful analysis of multiple data points. Looking at maintenance records, performance trends, and projected expenses gives you the full picture needed for planning. You’ll also want to factor in advances in vehicle technology, potential fuel savings from newer models, and expected resale values. For example, if a new vehicle offers significantly better fuel economy, the higher upfront cost could be offset by lower operating expenses within a few years. Taking all these elements into account helps you develop a renewal strategy that keeps costs down while maximizing vehicle availability.
Real-World Examples and Practical Methods
The best way to understand these concepts is through real examples. Consider a delivery company struggling with frequent breakdowns in their aging trucks. By reviewing repair records and calculating future maintenance costs, they determined that buying new vehicles would save money long-term by reducing repair expenses and improving delivery reliability. This shows how good data analysis leads to better fleet decisions. Regular review and updates to your strategy ensure you stay responsive to changes in vehicle technology and maintenance practices. The key is using concrete information to guide choices that benefit your organization’s bottom line.
Harnessing Data for Maintenance Excellence
Smart fleet maintenance requires going beyond basic service records to gather deep insights from operational data. By analyzing maintenance patterns, vehicle performance metrics, and repair histories, fleet managers can make better decisions about resource allocation and preventive maintenance schedules. Many organizations are now seeing significant cost savings and efficiency gains by taking a data-focused approach to fleet maintenance.
Implementing Key Performance Indicators (KPIs)
The foundation of data-driven maintenance starts with tracking the right metrics. Key performance indicators like vehicle downtime, cost per mile, and preventive maintenance compliance give fleet managers a clear view of their operation’s health. For instance, carefully monitoring downtime data helps identify recurring issues and their root causes. This allows managers to take targeted action rather than making decisions based on incomplete information or assumptions. The insights from these KPIs guide smart improvements to maintenance programs.
Building Meaningful Maintenance Dashboards
Data becomes truly useful when presented in an easy-to-understand format. Well-designed maintenance dashboards bring together important metrics in one place, making it simple to spot trends and potential problems. For example, if tire replacements suddenly increase on certain routes, the dashboard makes this pattern immediately visible. By combining data from maintenance records, telematics systems, and other sources, these dashboards give fleet managers a complete picture of their operations. This helps them catch and address issues early before they become major problems.
Using Predictive Analytics to Prevent Breakdowns
Advanced data analysis takes maintenance planning to the next level by forecasting future repair needs. By studying past maintenance records and vehicle performance data, predictive analytics can identify when components are likely to fail. This allows managers to schedule repairs at convenient times, avoiding unexpected breakdowns that disrupt operations. For example, if data shows a particular engine part typically fails after 50,000 miles, it can be replaced during regular service rather than waiting for it to break down. This proactive approach helps fleets run more reliably while controlling costs.
Selecting and Implementing Maintenance Management Systems
Finding the right software is essential for managing maintenance data effectively. The ideal system should handle data collection, analysis, and reporting while integrating with other fleet management tools. Key features to look for include automated reporting, maintenance alerts, and telematics integration. Auto Service Logger offers these capabilities in an easy-to-use platform that works well for fleets of any size. A careful, step-by-step implementation process - starting with data migration and staff training - helps ensure the system delivers value quickly.
Ready to improve your fleet maintenance with smart data tools? See how Auto Service Logger can help optimize your operations and reduce costs. Visit Auto Service Logger now!