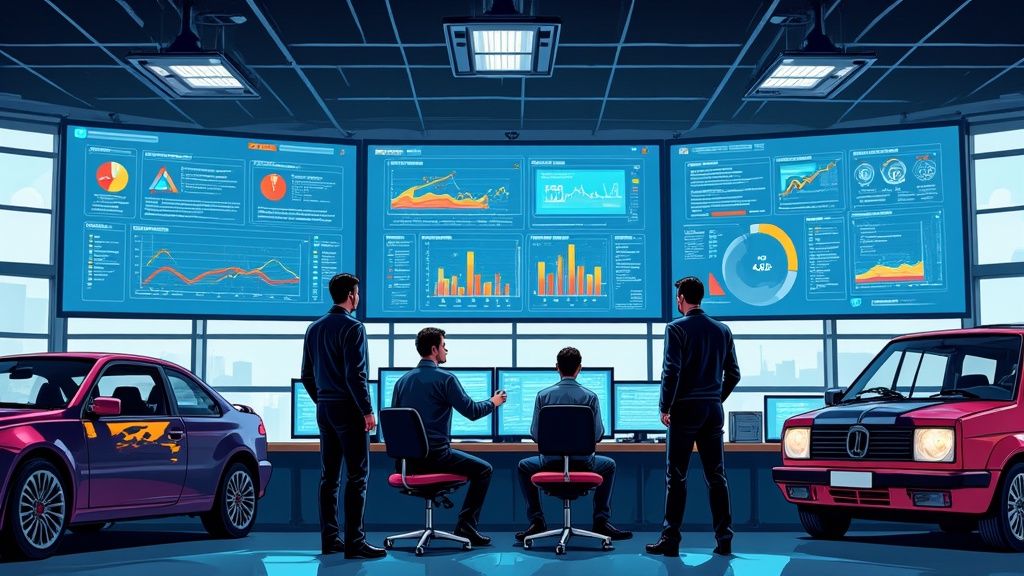
Fleet Maintenance Management: A Modern Guide to Transformation
Building a Proactive Maintenance Strategy That Works
Managing a fleet requires more than basic vehicle upkeep - it demands careful planning and foresight. Making the switch from fixing problems after they occur to preventing them in advance is key for any fleet operation. This preventive approach helps keep vehicles running smoothly while avoiding costly disruptions.
Understanding the Shift: Reactive vs. Proactive
While emergency repairs can’t always be avoided, relying solely on reactive maintenance leads to problems. When a delivery truck breaks down mid-route, it creates a chain reaction - missed deliveries, unhappy customers, expensive repairs, and potential safety risks. A proactive strategy helps prevent these issues through regular inspections and early problem detection. Simple steps like checking tire pressure routinely can prevent blowouts, extend tire life, save money, and keep drivers safe on the road.
Implementing a Proactive Fleet Maintenance Management Plan
Moving to proactive maintenance involves several key elements. Start by creating a detailed maintenance schedule based on manufacturer guidelines, how vehicles are used, and operating conditions. Clearly outline specific tasks, timing, and who’s responsible. Consider using Auto Service Logger or similar software to automate scheduling, track repairs, and analyze data. This organized system lets managers stay ahead of maintenance needs efficiently.
The Benefits of Proactive Maintenance
A well-executed proactive strategy delivers clear advantages. Research shows preventive maintenance can cut breakdowns by up to 45%, directly improving vehicle availability and productivity. This means more vehicles making deliveries instead of sitting idle for repairs. Early problem detection also reduces costs significantly - one study found companies using fleet management software saved an average of $100 per vehicle annually on maintenance. For large fleets, these savings add up quickly.
Engaging Your Team
Success requires participation from everyone involved. Technicians need proper training and tools to handle maintenance effectively. Clear communication and established procedures help ensure consistency and accountability. When staff understand why proactive maintenance matters and their role in it, operations run more smoothly. This team-based approach improves efficiency while building a culture focused on safety and responsibility - key factors in getting the most value from your fleet investment.
Maximizing ROI Through Strategic Planning
While having a proactive maintenance program is essential, achieving the best return on investment requires thoughtful strategic planning that considers every financial aspect of fleet operations. Companies that take this comprehensive approach are seeing impressive results - many have reduced their total ownership costs by up to 40% through careful fleet maintenance management.
Budget Optimization for Fleet Maintenance
Creating an effective budget requires more than just setting aside funds - it demands strategic allocation of resources. When presenting to stakeholders, highlight how preventive maintenance investments directly translate to long-term savings through fewer breakdowns and extended vehicle life. Look for hidden opportunities to reduce costs, such as bulk parts purchasing agreements or implementing driver training to improve fuel efficiency. These targeted efforts can significantly boost your bottom line.
Balancing Cost Control With Service Quality
The key is finding the right balance between minimizing expenses and maintaining excellent service levels. Focus on high-impact preventive maintenance that keeps vehicles running reliably while avoiding unnecessary repairs. For example, thorough routine maintenance can substantially extend vehicle lifespans, reducing the frequency of expensive replacements. This allows you to redirect funds to critical areas like safety programs and driver development.
Strategies for Reducing Fuel Consumption
As one of the largest operational expenses, fuel costs demand special attention in any fleet management strategy. Basic maintenance like clean air filters and proper tire pressure directly impacts fuel economy. Consider investing in fuel-efficient vehicles and implementing driver training focused on economical driving techniques. Over time, these efforts can generate substantial cost savings.
Extending Vehicle Lifespans Through Strategic Maintenance
Getting maximum value from each vehicle requires a well-planned approach to maintenance. A robust preventive program built on regular inspections, timely repairs, and manufacturer-recommended service intervals helps vehicles last longer and perform better. This proactive stance protects your fleet investment in several key ways:
- Data-Driven Decisions: Use fleet management systems to analyze maintenance records, spot patterns, and make informed choices about repairs and replacements.
- Driver Engagement: Create clear processes for drivers to report issues quickly and participate in regular vehicle care training.
- Continuous Improvement: Review maintenance data and feedback regularly to refine your approach. Small adjustments based on real results can lead to major improvements.
Strategic fleet maintenance is an ongoing process that requires constant attention and refinement. By consistently monitoring results and adjusting your approach, you can keep your fleet operating efficiently while maximizing returns. This balanced focus on both immediate needs and long-term planning helps ensure sustainable financial performance.
Leveraging Technology Without Breaking the Bank
Effective fleet management starts with solid planning and maintenance. But to truly improve operations and stay competitive, the right technology makes all the difference. Rather than chasing every new gadget, successful fleet maintenance depends on selecting tools that actually fit your specific operation and budget constraints.
Choosing the Right Tools for Your Fleet
Today’s fleet maintenance technology offers several key options worth considering. Telematics systems provide real-time data on vehicle location, speed, fuel use, and driver behavior - helping managers spot opportunities to improve fuel efficiency, routes, and driver training. Maintenance software like Auto Service Logger makes it easier to schedule maintenance, track repairs, and analyze fleet data for better decision-making. Diagnostic tools speed up troubleshooting and cut repair costs by quickly pinpointing issues.
Integrating Technology for Seamless Operations
The real value comes from connecting these tools together. For example, when telematics data feeds directly into maintenance software, it can automatically trigger service alerts based on mileage or engine hours. This eliminates manual tracking and ensures timely maintenance before problems occur. When information flows smoothly between systems, managers can make faster, more informed decisions.
Avoiding Implementation Pitfalls and Ensuring User Adoption
Simply buying new technology isn’t enough - implementation requires careful planning. Without proper training and support, staff may resist using new systems, negating their benefits. Focus on choosing user-friendly tools that integrate well with your existing processes. Provide thorough training so your team understands how to use the technology effectively. Start with the basics and gradually expand capabilities as users become more comfortable.
Real-World Results: How Technology Impacts the Bottom Line
The financial impact of smart technology use is clear. Studies show fleet management software saves an average of $100 per vehicle annually on maintenance costs alone. Companies using telematics report up to 55% lower fuel expenses through improved routing, reduced idling, and better driving habits. By preventing breakdowns and minimizing repair time, these tools keep more vehicles on the road generating revenue. For fleets looking to stay competitive and profitable, the right technology is now essential for effective maintenance management.
Building Your Dream Maintenance Team
Behind every successful fleet maintenance program is a skilled and dedicated team. While modern technology provides valuable tools, it’s the human element that makes the real difference. Building and maintaining a strong technical team requires careful attention to hiring, training, and creating an environment where people can excel.
Recruiting Top Talent: Finding the Right Fit
Finding skilled technicians takes more than posting job listings. To attract top talent, fleet managers need to build relationships with technical schools and training programs to connect with promising candidates early in their careers. Offering competitive pay and benefits is also essential - skilled technicians have many options in today’s job market, so your compensation needs to stand out.
Effective Training Programs: Investing in Your Team
Once you’ve built your core team, ongoing training helps keep their skills sharp. Regular training sessions should cover new repair methods, diagnostic tools, and safety procedures. For example, when technicians learn to use the latest diagnostic equipment properly, they can pinpoint issues faster and reduce repair times. Supporting technicians in earning industry certifications also shows you’re invested in their growth while expanding their capabilities.
Creating a Culture of Continuous Improvement
Strong technical skills are important, but a positive work environment helps retain valued team members for the long run. Encourage open communication, act on feedback, and recognize good work. Set up systems for technicians to share tips and lessons learned from complex repairs. When people feel their input matters and they’re part of a collaborative team, job satisfaction and retention typically improve.
Measuring Performance and Driving Results
Clear performance tracking helps identify both successes and areas needing attention. Monitor key metrics like vehicle uptime, repair completion times, and maintenance costs. Use data from tools like Auto Service Logger to spot trends - if certain vehicle types consistently need expensive repairs, that may indicate a need for focused training. Regular performance reviews with constructive feedback empower your team to keep improving and contribute more effectively to your fleet’s success.
Implementing Lean Practices That Actually Work
Creating a high-performing maintenance operation requires more than just having skilled technicians and modern technology. What really sets top fleets apart is their disciplined application of Lean principles, adapted from manufacturing to address the specific needs of fleet maintenance. This proven approach focuses on delivering maximum value while eliminating wasteful activities that drain resources and slow down operations.
Identifying and Eliminating Waste in Fleet Maintenance
In fleet maintenance, waste takes many forms that directly impact productivity and costs. The classic TIMWOOD framework helps identify seven key areas where waste commonly occurs. For instance, vehicles making unnecessary trips between repair facilities wastes transportation resources. Parts sitting unused for months tie up inventory space and capital. Technicians spending time searching for misplaced tools represents wasted motion. Vehicles sitting idle while waiting for parts or available technicians means lost productivity. Running preventive maintenance more frequently than needed consumes extra labor hours. Complex paperwork processes bog down operations. And faulty repairs that require rework compound costs and downtime. By methodically examining each of these areas, maintenance managers can spot opportunities to streamline their operations.
Practical Tools and Techniques for Lean Implementation
Several proven Lean methods help maintenance teams eliminate waste and improve efficiency. Value stream mapping creates a detailed visual representation of each maintenance process step, from initial inspection through final repair completion. This helps teams spot bottlenecks and steps that don’t add value. The “5 Whys” root cause analysis digs deeper to uncover underlying issues behind recurring problems. For example, if a certain truck model keeps having brake failures, simply replacing parts treats the symptom. Root cause analysis would investigate why those brakes fail repeatedly, potentially revealing deeper issues like design flaws or improper usage patterns.
Step-by-Step Implementation Guide for Lean Fleet Maintenance
Successfully adopting Lean maintenance requires a systematic approach. The first step is forming a cross-functional team representing maintenance operations at all levels. This team needs thorough training in Lean concepts and methods. Next, they should assess current maintenance processes through data analysis and direct observation of daily workflows. The data shows what’s happening, but watching operations unfold reveals the “why” behind the numbers. Based on this assessment, the team can prioritize improvement projects with the highest potential impact. They then use Lean tools like value stream mapping and root cause analysis to implement targeted changes. Regular monitoring helps measure results and refine the approach. For example, after introducing a new parts inventory system, track how it affects repair wait times and storage costs. These metrics guide ongoing adjustments. Through this disciplined process, maintenance operations can steadily eliminate waste and build more efficient practices.
Future-Proofing Your Maintenance Operations
To keep up with the ever-changing transportation industry, fleet maintenance managers must adapt and plan ahead. Success depends on implementing new technologies and processes in a strategic way that improves operations both now and in the future.
Embracing Emerging Technologies
The maintenance field is seeing major advances in areas like predictive analytics, artificial intelligence (AI), and the Internet of Things (IoT). These tools help fleets work smarter - predictive analytics spots potential vehicle issues before they cause breakdowns, while AI automates scheduling and route optimization based on real-time data. IoT sensors placed on vehicles continuously monitor critical metrics like tire pressure and engine performance, giving maintenance teams early warnings about developing problems. For example, if a sensor detects unusual engine temperatures, technicians can investigate before it leads to a serious malfunction.
Evaluating and Implementing New Technologies
While these advances offer real benefits, choosing the right tools requires careful evaluation. Fleet managers need to assess how well new technologies match their specific needs and budget constraints. A small local fleet, for instance, may not need the same advanced telematics system that benefits long-haul trucking operations. The key is selecting solutions that align with business goals and deliver clear value. Consider factors like:
- Your fleet size and vehicle types
- Existing systems and infrastructure
- Implementation costs and complexity
- Expected return on investment
Developing Adaptive Maintenance Strategies
Beyond just adopting new tools, fleets need flexible strategies that can evolve over time. This starts with creating a culture of continuous learning and improvement. Give technicians opportunities to explore emerging technologies through training and hands-on experience. Regular reviews of maintenance data and industry trends help identify areas for optimization. The goal is building an approach that can adapt as needs change and new solutions emerge.
Frameworks for Assessing New Technologies
Creating a structured evaluation process helps make smart technology decisions. Start with pilot programs to test promising solutions on a smaller scale first. This provides real-world performance data and surfaces potential issues early. Include maintenance staff in the assessment - their practical experience offers valuable insights about what works. Key evaluation criteria should cover:
- Implementation requirements and complexity
- Integration with current systems
- Total costs versus expected benefits
- Staff training needs
- Measurable performance improvements
Ready to bring your fleet maintenance into the future? Auto Service Logger helps you track, manage, and optimize your maintenance operations with ease. Start your free trial today and discover how Auto Service Logger can help you future-proof your fleet: https://autoservicelogger.com/