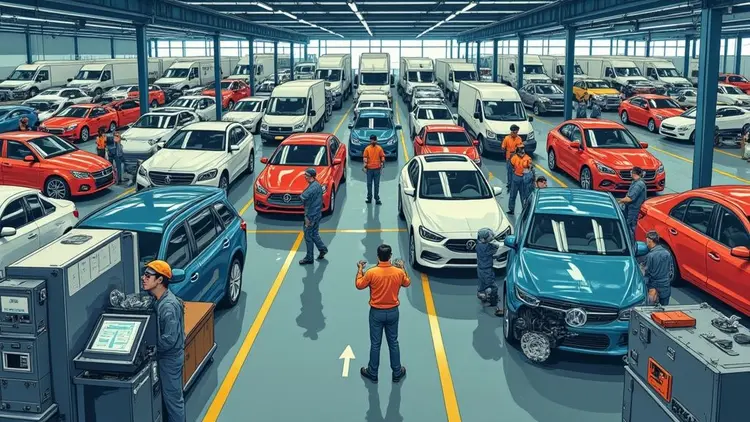
The Complete Guide to Vehicle Fleet Maintenance: Proven Strategies for Peak Performance
Current Trends in Fleet Maintenance
The automotive repair and maintenance sector continues expanding, with projections showing the global market reaching $1.381 billion by 2028. This growth stems from increased vehicle failure rates, the financial benefits of repairing older vehicles instead of replacing them, and stricter government regulations on automotive waste. For fleet managers, this means proper maintenance is more important than ever as they work to keep vehicles running efficiently while controlling costs.
Managing Rising Costs and Parts Availability
Fleet maintenance faces significant challenges from increasing repair expenses and ongoing parts shortages. Some segments of the industry experienced repair cost increases of up to 20% in early 2023. These higher costs partly result from keeping aging vehicles in service longer due to limited new vehicle availability. As a result, fleets now deal with more major repairs like engine and transmission work. This requires fleet managers to carefully plan their maintenance approach and budgets.
Finding the Right Maintenance Balance
Successful fleet operations require carefully balancing scheduled maintenance with unexpected repairs. While a strong preventive maintenance program helps avoid many breakdowns, emergency repairs remain unavoidable. Accidents and sudden part failures demand quick responses, making relationships with reliable repair shops and parts suppliers essential. Fleet managers must constantly evaluate how to best divide resources between prevention and repairs to minimize vehicle downtime.
Maintaining Aging Vehicle Fleets
Older vehicles in fleets significantly impact maintenance costs and planning. These aging vehicles need more frequent repairs and replacement parts that may be harder to source. To manage this effectively, fleet managers must closely track each vehicle’s maintenance history and address potential issues early. Auto Service Logger provides digital tools that help organize maintenance records in one place, allowing managers to spot patterns and make informed decisions about repairs versus replacement.
Electric Vehicle Maintenance Considerations
As more fleets add electric vehicles (EVs), they face different maintenance needs. While EVs typically require less routine maintenance than conventional vehicles, they present unique challenges. Their heavier weight leads to faster tire and brake wear, increasing certain maintenance costs. EVs also need specialized service procedures and often must return to dealers for repairs. However, manufacturer warranties currently cover many EV repairs, helping offset some expenses. As EVs become more common in fleets, maintenance practices will need to adapt to their specific requirements.
Building a Preventive Maintenance Program That Actually Works
Smart fleet managers know that waiting for vehicles to break down before fixing them is a costly mistake. By shifting from reactive repairs to preventive maintenance, companies can significantly reduce vehicle downtime and extend the life of their fleet. While building an effective preventive maintenance program takes work, the long-term benefits make it well worth the effort.
Key Components of an Effective Program
A successful preventive maintenance program starts with establishing clear maintenance schedules based on manufacturer guidelines and your fleet’s specific operating conditions. For instance, vehicles that regularly carry heavy loads or operate in harsh environments need more frequent service compared to those used for lighter duty.
Detailed checklists are another essential element. These should outline all required inspections and services - from checking fluid levels to examining brakes, tires, belts and hoses. But creating checklists isn’t enough - maintenance teams need proper training to use them consistently and document their findings thoroughly. This documentation builds a valuable service history for each vehicle that helps identify recurring issues before they become major problems.
Managing Diverse Vehicle Types and Maintenance Intervals
Fleet managers face a particular challenge when maintaining different types of vehicles, since each has its own maintenance requirements and service intervals. Rather than taking a generic approach, create customized maintenance schedules for each vehicle category. This ensures every vehicle gets exactly the service it needs at the right time.
Digital tools like Auto Service Logger can help streamline maintenance tracking across diverse fleets. These platforms automatically track service intervals, send maintenance reminders, and maintain detailed vehicle records. This systematic approach helps prevent missed services that could lead to costly repairs.
Identifying Potential Issues and Scaling Your Program
A key advantage of preventive maintenance is spotting problems early through data analysis. By tracking repair frequency and costs over time, patterns often emerge that point to systemic issues. For example, if multiple vehicles need the same part replaced frequently, it may indicate a design flaw or maintenance gap that needs addressing.
As your fleet grows, your maintenance program must evolve to handle increased complexity. Having scalable systems and processes in place - particularly fleet management software - allows you to efficiently manage more vehicles without sacrificing service quality. The software can automate routine tasks, streamline workflows, and provide data insights to continuously optimize your program. While implementing comprehensive preventive maintenance requires upfront investment, it delivers clear returns through reduced repair costs, less downtime, and improved fleet reliability.
Mastering Electric Vehicle Fleet Maintenance
Running a fleet of electric vehicles (EVs) requires a fresh approach to maintenance compared to traditional gas-powered vehicles. While EVs have fewer moving parts and typically need less routine upkeep, they come with their own set of maintenance requirements that fleet managers must understand to keep vehicles running efficiently and minimize time out of service.
Addressing Unique EV Maintenance Needs
EVs bring distinct maintenance considerations that differ from conventional vehicles. For instance, their regenerative braking systems reduce—but don’t eliminate—wear on friction brakes, meaning brake inspections are still needed, just less often. The heavy battery packs in EVs can also cause tires to wear more quickly, calling for more frequent tire rotations and replacements. Being aware of these key differences helps fleet managers develop effective maintenance schedules.
Battery Health and Management
The battery system is critical to EV performance and longevity. Just as regular oil changes were essential for gas vehicles, proper battery care is fundamental for EVs. This includes following recommended charging practices, protecting batteries from temperature extremes, and using diagnostic tools to track battery health metrics. Regular monitoring helps catch potential issues early and ensures optimal range and performance throughout the battery’s life.
Training and Expertise for EV Maintenance
Working on EVs requires specialized knowledge that differs from traditional vehicle repair. Technicians need specific training to safely work with high-voltage systems and accurately diagnose issues with electric motors and battery components. By investing in comprehensive training programs, fleet managers ensure their maintenance teams can handle EV-specific repairs safely and efficiently, reducing vehicle downtime.
Optimizing Charging Infrastructure for Fleet Needs
A well-planned charging system is essential for keeping an EV fleet moving. This means carefully choosing charger locations and types to match your fleet’s operational patterns. Key decisions include selecting between Level 2 and Level 3 chargers, determining optimal charging speeds, and ensuring reliable network connections. Integrating charging data with fleet management systems provides useful insights about energy use and charging patterns. Just as gas fleets need dependable fuel access, EV fleets require reliable charging infrastructure to maintain smooth operations and minimize idle time between routes.
Using Technology to Improve Vehicle Maintenance
Modern technology gives fleet managers powerful tools to shift from reactive to proactive maintenance approaches. With the right technology solutions in place, managers can analyze data to make informed decisions about service timing, resource allocation, and cost management. But success requires carefully selecting and implementing tools that match your fleet’s specific needs.
Predictive Analytics: Seeing Problems Before They Happen
The ability to predict vehicle issues before they cause breakdowns is incredibly valuable. By examining historical data on maintenance records, mileage patterns, and operating conditions, analytics systems can identify early warning signs of potential problems. For instance, if the system flags that a truck’s brakes are likely to fail within 1,000 miles, managers can schedule maintenance before an expensive roadside breakdown occurs. This data-driven approach helps prevent disruptions while improving both safety and efficiency.
Telematics: Understanding Vehicle Health in Real Time
Telematics systems provide continuous data streams showing vehicle location, speed, fuel use, and engine diagnostics. This real-time visibility helps managers spot developing issues quickly. When integrated with maintenance software, telematics data can automatically trigger service reminders and track repair progress. The result is a seamless system where vehicle data directly guides maintenance decisions and scheduling.
Maintenance Software: Organizing Fleet Operations
Purpose-built software platforms like Auto Service Logger serve as command centers for fleet maintenance activities. These tools help managers schedule preventive service, monitor repair costs, manage parts inventory, and generate detailed reports. Many platforms also include mobile access for technicians and communication tools for coordinating with vendors. With all maintenance data and workflows in one place, teams can work more efficiently and stay better aligned.
Implementing New Technologies: Taking a Measured Approach
Adding new technology requires careful planning. Start by clearly defining your fleet’s challenges and goals. Research solutions that specifically address those needs rather than chasing trendy features. Test new systems with a small pilot program first to work out any issues. Once the pilot succeeds, gradually expand across your full fleet while providing thorough staff training. This step-by-step method minimizes disruption and helps ensure effective adoption of new maintenance tools and processes.
Controlling Costs Without Compromising Quality
A well-run vehicle fleet requires carefully balancing operational needs with financial constraints. Like a skilled chef who knows exactly which ingredients to use and in what proportions, fleet managers must make strategic decisions about maintenance spending that keep vehicles running smoothly without unnecessary expenses. Success comes from finding the right mix of quality parts, skilled labor, and reliable vendors.
Optimizing Vendor Relationships and Parts Procurement
Building strong partnerships with repair shops and parts suppliers is essential for managing costs. When fleet managers develop good working relationships with vendors, they often gain access to bulk pricing discounts, faster service times, and higher quality work. For instance, a trusted parts supplier may offer 15-20% off commonly replaced items when purchased in volume. Creating formal vendor agreements also reduces time spent shopping around for parts and negotiating prices.
Smart parts procurement goes beyond just vendor relationships. Fleet managers can often find significant savings by using quality aftermarket or remanufactured parts for certain repairs instead of new OEM components. This requires carefully evaluating each situation - a remanufactured starter motor might work perfectly well at half the cost of new, while safety-critical parts may warrant original equipment. The key is knowing when alternative parts make sense and when they don’t.
Streamlining Labor Allocation and Maintenance Schedules
Getting the most value from maintenance labor is another critical factor. Well-trained technicians who have the right diagnostic tools and equipment can complete repairs more efficiently, reducing both labor costs and vehicle downtime. Investing in technician training and proper tools pays off through faster, more accurate repairs. For example, a diagnostic scanner that quickly pinpoints problems can save hours of troubleshooting time.
Following consistent maintenance schedules is equally important for controlling costs. Regular preventive maintenance like oil changes, filter replacements, and thorough inspections helps catch small issues before they become expensive problems. This proactive approach reduces surprise breakdowns and extends vehicle life. Just as regular dental cleanings prevent cavities, staying on top of routine vehicle maintenance prevents many costly repairs down the road.
Evaluating Maintenance Investments and Managing Emergency Repairs
Each maintenance decision represents a financial investment that needs careful evaluation. As vehicles age, fleet managers must analyze repair costs versus replacement value to make smart choices. Sometimes it makes more sense to replace an older vehicle than sink money into major repairs. Good data tracking of maintenance history and costs for each vehicle provides the insights needed for these decisions.
Even with excellent preventive maintenance, emergency repairs will occasionally be needed. Having established procedures and relationships with repair shops helps control these unexpected costs. Setting aside dedicated funds for emergency repairs provides a financial buffer. Clear protocols for handling unexpected repairs, combined with pre-negotiated service rates, help minimize both costs and disruption when issues arise. With the right mix of proactive maintenance, strategic vendor partnerships, and emergency preparedness, fleet managers can effectively control costs while keeping vehicles running reliably.
Building a Future-Ready Maintenance Strategy
To keep any fleet running smoothly, maintenance strategies must adapt to changing technologies and industry demands. Establishing a solid foundation today helps ensure your fleet stays efficient and cost-effective as new developments emerge. By creating flexible systems and processes, you can better position your fleet for success in the years ahead.
Preparing for the Rise of Electric Vehicles
As more fleets incorporate electric vehicles (EVs), maintenance needs are shifting significantly. While EVs typically need less regular maintenance compared to traditional vehicles, they introduce their own set of challenges. Their heavier battery packs often cause tires and brakes to wear more quickly, requiring more frequent replacements. What’s more, servicing high-voltage systems demands specialized training and equipment. Fleet managers need to invest in developing technician skills and updating service facilities to properly maintain EVs.
Embracing Advanced Diagnostics and Predictive Maintenance
Data and technology are becoming essential tools for modern fleet maintenance. Advanced diagnostic systems paired with telematics allow managers to spot potential issues early. For instance, sensors can detect unusual engine vibrations and alert managers to schedule preventive service before a breakdown occurs. This shift from reactive repairs to data-driven preventive maintenance helps minimize downtime, extend vehicle life, and reduce overall costs.
Adapting to Alternative Fuels and Technologies
Beyond electric vehicles, other new technologies are entering the fleet landscape. Hydrogen fuel cell vehicles, self-driving systems, and connected vehicle platforms each require specific maintenance approaches. Managers should stay informed about these developments and incorporate them into long-term planning. This often means building relationships with specialized service providers and creating new training programs. For example, maintaining hydrogen fuel cells requires different expertise than traditional vehicle repair.
Developing a Flexible and Scalable Maintenance Strategy
An effective maintenance strategy must be able to grow and change over time. Key elements include:
- Continuous Learning: Following industry trends and maintenance best practices
- Flexible Processes: Creating procedures that can adapt to different vehicle types
- Scalable Systems: Using software that can handle increasing fleet complexity
- Strategic Partnerships: Working with vendors who provide specialized expertise
By focusing on these areas, fleet managers can build maintenance programs ready to handle both current needs and future changes. This forward-looking approach helps control costs while keeping vehicles running reliably.
Ready to take control of your fleet maintenance and prepare for the future? Auto Service Logger offers a comprehensive platform to streamline your maintenance records, track vehicle health, and make data-driven decisions. Start your free trial today and experience the benefits of a digital maintenance solution: https://autoservicelogger.com/